You have reached your limit of 3 free stories. A story preview is shown instead.
To view more stories
(If your subscription is current,
click here to Login or Register.)
They Wash And Spin Greens Clean
Prepping 50 lbs. of salad greens is a big job if you don’t have the right tools. Matthew Jose found a way to do it with a big washing tank and a spinner.
“Cooling down and washing greens is a market gardener’s bottleneck,” says Jose, who runs a year-round organic production company in Indianapolis, Ind., with hi
..........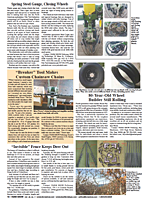
You must sign in, subscribe or renew to see the page.
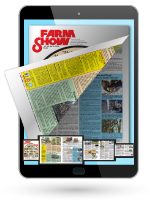
You must sign in, subscribe or renew to see the flip-book
They Wash And Spin Greens Clean CROPS Miscellaneous Prepping 50 lbs of salad greens is a big job if you don’t have the right tools Matthew Jose found a way to do it with a big washing tank and a spinner “Cooling down and washing greens is a market gardener’s bottleneck ” says Jose who runs a year-round organic production company in Indianapolis Ind with his business partner Amy Matthews They used to put greens in 2-lb mesh bags and move them through three rinse tanks After drip-drying for a time they’d be spun out in a hand spinner a pound of greens at a time “The system placed a surprising strain on our backs and the hand crank salad spinner wasn’t a sustainable tool for processing up to 200 lbs of salad greens per week ” recalls Jose They needed a low-cost efficient greens processing system Their new wash station is enclosed in double-walled greenhouse plastic with landscape fabric topped by gravel for a floor Hand-built worktables handle incoming and outgoing greens The heart of the washing system is a 100-gal stock tank with a bubbler system Greens are added to the stock tank for a quick cool down and rinse They’re then transferred in approximately 2 lb lots to plastic mesh baskets The baskets are sized to fit a converted washing machine After drip-drying for a few minutes in an empty stock tank they’re moved to the spinner After a 2-min spin they’re transferred to a clean tote “We purchased a greens bubbler tutorial from Dry Your Greens www dryyourgreens com and modified it ” says Jose “It included plans for how to build a bubbler and how to convert the washer to a spinner ” Jose’s bubbler uses a 1 hp blower he bought at a Jacuzzi supply store to blow air through a pvc tube system lined with holes An industrial sink drain and an attached flexible pipe drain away wash water Jose and Matthews used a Whirlpool Cabrio model washing machine that met the specifications in the tutorial At the time they also purchased a parts kit for the conversion from Dry Your Greens “Our system with one bubbler and the spinner works well for us ” says Jose “If we did more than we do now we might want a second bubbler tank However the one spinner would still be sufficient ” Jose likes the increased productivity of the wash station which cut greens washing/drying time in half He and Matthews also appreciate the opportunity to multi-task “We have the bubbler and the spinner set on timers ” he says “This allows the operator to start the process and do other tasks while the greens are bubbling or spinning ” Jose developed the system with the help of a $6 000 SARE grant Contact: FARM SHOW Followup Mad Farmers Collective 2052 S Meridian St Indianapolis Ind 46225 ph 317-446-9448; matthew@bigcityfarmsindy com; www madfarmerscollective com; www facebook com/madfarmerscollective
To read the rest of this story, download this issue below or click
here to register with your account number.