100-Ton Shop-Built Press Brake
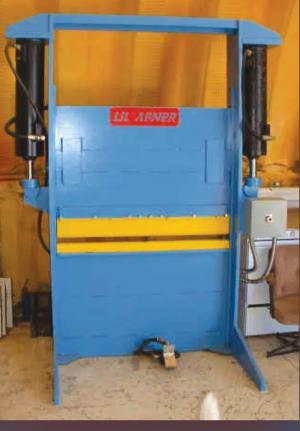 ✖  |
Pat Burrington says he couldn’t justify spending a bundle of money on a high-capacity press brake for his welding shop, so he built one himself. “I built it several years ago when steel wasn’t nearly as costly as it is today, so my investment was probably a third of what it would’ve cost to buy one,” Burrington says.
He made the frame and side pieces for the 100-ton brake using 40 ft. of 12-in. wide by 1-in. thick flat bar steel, stacked vertically for added strength. “I water jetted all the critical pieces like the slides and notches, then flux core welded it all together,” Burrington says.
He bought the 7-in. dia. press cylinders, hoses and hydraulic pump from the Surplus Center in Lincoln, Neb. A friend gave him a 3-hp. electric motor and pump, which produces 2,500 psi of working pressure, to operate the press.
“I didn’t think I could fabricate the upper and lower dies, so I bought those from a manufacturer’s rep I met at the Fabtech trade show in Chicago. Those worked perfectly, and I’ve used them to bend all types of metal, even water flumes and custom high-strength cardboard boxes. I even made a set of dies to punch in/out the pins and bushings on my Deere MC crawler track instead of having the dealer do it,” Burrington says.
For a total cash outlay of about $4,000 plus his labor, Burrington says his custom-built press brake was a worthwhile investment that’s paid for itself many times. “Better yet, if anything goes wrong, which it rarely has, I know exactly how to fix it and don’t need to call for repairs,” he adds.
Contact: FARM SHOW Followup, Pat Burrington, Rapid Creek Cutters, 130 Garnet Dr. Hwy 93, Stevensville, Mont. 59870 (ph 406-642-3155; www.rapidcreekcutters.com).
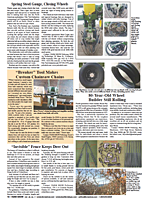
Click here to download page story appeared in.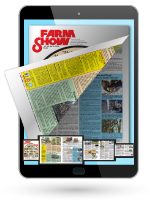
Click here to read entire issue
100-Ton Shop-Built Press Brake Pat Burrington says he couldn’t justify spending a bundle of money on a high-capacity press brake for his welding shop so he built one himself “I built it several years ago when steel wasn’t nearly as costly as it is today so my investment was probably a third of what it would’ve cost to buy one ” Burrington says He made the frame and side pieces for the 100-ton brake using 40 ft of 12-in wide by 1-in thick flat bar steel stacked vertically for added strength “I water jetted all the critical pieces like the slides and notches then flux core welded it all together ” Burrington says He bought the 7-in dia press cylinders hoses and hydraulic pump from the Surplus Center in Lincoln Neb A friend gave him a 3-hp electric motor and pump which produces 2 500 psi of working pressure to operate the press “I didn’t think I could fabricate the upper and lower dies so I bought those from a manufacturer’s rep I met at the Fabtech trade show in Chicago Those worked perfectly and I’ve used them to bend all types of metal even water flumes and custom high-strength cardboard boxes I even made a set of dies to punch in/out the pins and bushings on my Deere MC crawler track instead of having the dealer do it ” Burrington says For a total cash outlay of about $4 000 plus his labor Burrington says his custom-built press brake was a worthwhile investment that’s paid for itself many times “Better yet if anything goes wrong which it rarely has I know exactly how to fix it and don’t need to call for repairs ” he adds Contact: FARM SHOW Followup Pat Burrington Rapid Creek Cutters 130 Garnet Dr Hwy 93 Stevensville Mont 59870 ph 406-642-3155; www rapidcreekcutters com