1989 - Volume #13, Issue #2, Page #33
[ Sample Stories From This Issue | List of All Stories In This Issue | Print this story
| Read this issue]
Teeter Totter Drive Up Ramp For Cars, Trucks
"It works perfectly. If I were going to build another one I wouldn't change a thing," says Bruce Ogram, Elmira, Ontario who built an ingenious "teeter totter" drive-up ramp for car and truck maintenance that does the job of expensive hydraulic hoists but has the advantage of total portability.Ogram wanted to work under cars and trucks but he didn't have a good spot to build a permanent ramp. Also, he wanted to use the ramp to clean the undersides of vehicles with a high pressure washer and then to apply undercoating, and he wanted to be able to do that messy work in an out-of-the-way spot.
The unique "teeter totter" ramp he built is 30 ft. long and pivots at a point 17 ft. from the lower ramp end. The car or truck drives up the ramps, made out of 10-in. wide I-beams, and when it passes the pivot point it over-balances the ramp and drops it to the ground. The fall of the ramp is cushioned by 20-in. truck tires. When the vehicle backs off, the rear end drops to the ground, also cushioned by tires.
"There's only a mild bump when it drops to the ground because if you drive slowly across the pivot point it'll drop slowly. The tires help cushion it as does the suspension system of the vehicle," says Ogram.
One of the I-beam tracks is anchored solidly to the ramp frame while the other track slides back and forth to fit varying wheel spacings. It'll narrow up enough to accommodate a garden tractor.
The main support legs are made from 61/ 2 by 8 by 3/8-in. H-beam. The top end legs are made from 2 1/2 by 10-in. channel iron. Bracing consists of 2-in. dia. pipe with flattened ends welded to the legs with 1/4-in. thick flat iron gussets. On the left side as you drive up the ramp there's a 2 by 6-ft. catwalk and ,,a ladder that swings out to dismount from the vehicle.
When a vehicle is in the raised position, it's approximately 5 ft. 6 in. above the ground. It could be built higher or lower as desired, says Ogram.
A 13-ft. by 10-in. I-beam serves as the pivot point, and it also slides out for use as the tongue for transport. The pivot beam is fitted with small cast iron wheels so it can be rolled from the pivot to the lower end of the ramp to be put in place for transport. Moving and mounting the tongue is an easy one-man job with the use of hydraulic jacks.
There's a low railing along each side of the tracks - 6 in. above the bottom of the track - that keeps the tires on track. A strip of expanded metal grating laid into each track provides good traction even when wet or covered with snow. A 6-in. piece of angle iron across the end of each track acts as a "stop,,.
To get onto the ramp, two hinged 4-ft. long, 10-in. wide channel iron tracks extend to the ground from the bottom of the ramp resting on the truck tire cushions.
"We've taken the ramp on the highway pulling it behind our Ford Econoline van. Transport width is 8 ft., 6 in. We had no more problem than pulling a load of hay," says Ogram, who says the ramp weighs 5,865 lbs. although it's balanced so that tongue weight is no more than 115 lbs. Total cost of construction was $1,162.68, using mostly scrap materials, and it took 177 hrs. of shop time.
The biggest vehicle Ogram has driven onto the ramp is his Ford van but he says it'll handle bigger pickups and trucks.
For more details, send a stamped envelope to: FARM SHOW Followup, Bruce Ogram, Rt. 4, Elmira, Ontario Canada N3B 2Z3 (ph 519 669-3771)
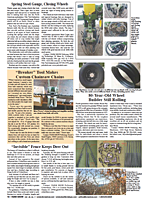
Click here to download page story appeared in.
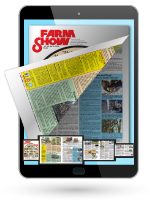
Click here to read entire issue
To read the rest of this story, download this issue below or click here to register with your account number.