2023 - Volume #47, Issue #1, Page #17
[ Sample Stories From This Issue | List of All Stories In This Issue | Print this story
| Read this issue]
“Bear Cub” Has Power To Spare
![]() |
![]() |
“In low gear, it pushes dirt like a bulldozer,” says Rawls. “It’ll really dig in second gear. People used to call me Bear, so I call it the ‘Bear Cub.’”
The old Cub had been sitting in the trees when Rawls decided to fix it up. It had some rainwater in it, so he took it apart, checked all the gears and bearings and flushed the transmission.
“The transmission and the rear end on the Cubs are made out of good stuff,” says Rawls. “I wanted to make use of them.”
The motor was shot, so he replaced it with a 6-hp. engine from Harbor Freight. He had to turn it backward to match the drive with the Cub. He also mounted a centrifugal clutch salvaged from an IH 404 on the front of the engine.
“I made a jackshaft to run from the drive on the front of the engine to the transmission behind it. It is about 2 ft. long and runs under the engine with a universal joint connecting it to the transmission.”
Rawls mounted the engine to an aluminum plate and put it on stilts bolted to the frame to provide room for the driveshaft. He mounted a pulley to the driveshaft just a little smaller than the large pulley on the centrifugal clutch and connected them with a belt. A lever on the left side of the Cub brakes the centrifugal clutch.
“When I want to change gears, I just pull back on the brake lever,” says Rawls.
Initially, he had planned to add a power steering hydraulic pump to the Cub, but opted instead for a hydraulic pump, also salvaged from the 404. That required he extend the driveshaft on the engine to mount a small pulley.
“I machined the pulley and a keyway on it, fit it together on the shaft and tightened it up,” recalls Rawls. “It ran within perhaps 10/1000s of true, which was enough for me.”
The pump was overkill, and he knew he had to gear it down. He used an 8-in. pulley on the pump and connected the two with a belt.
“The pump has more pressure and flow than the engine can handle,” says Rawls. “Even with gearing it down, it sometimes kills the engine.”
The pump came with two 1 1/2-in. cylinders and a valve set with a diverter. He mounted one cylinder in the middle of the tractor to raise and lower a front blade. The other cylinder was mounted in the back to raise and lower a homemade set of 3-pt. arms.
“I added a third cylinder on the back, so there was a cylinder on each lift arm,” says Rawls.
The final touch for the hydraulics system was a reservoir. He fabricated it out of 1/8-in. steel and put a filter and hoses on it. He mounted it over the pump at the front of the tractor and added a relief valve to the system.
“When I let off the lever, it recirculates back to the tank,” says Rawls.
The hydraulics let him push dirt with a blade from a Deere 110 and use a landscape rake on the rear. The diverter lets him switch back and forth between the two.
The placement of the carburetor on the left side of the engine and the fuel tank on the right required a change to the hood. Rawls made it out of sheet metal.
“I also replaced the old Cub seat with a larger seat to accommodate me better,” says Rawls. “I hinged it to flip forward, which let me add a small toolbox under it. It’s been a really handy tractor. I can push up roots and fill in with soil with the rake.”
Contact: FARM SHOW Followup, William Rawls, 26362 NC Highway 210 E, Currie, N.C. 28435 (ph 910-669-2976; williamrawls7@gmail.com).
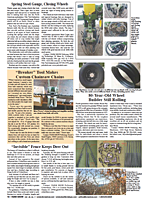
Click here to download page story appeared in.
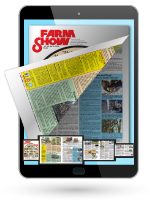
Click here to read entire issue
To read the rest of this story, download this issue below or click here to register with your account number.