Zapping Weeds With Lasers
Carbon Robotics is zapping weeds with lasers, saving high-value crop farmers time and money. The rear-mounted platforms carry eight laser modules. The simultaneously operating laser can kill more than 200,000 weed seedlings per hour while leaving desired seedlings untouched. First introduced in February 2022, production is sold out through the end of 2023.
“We are shipping them as fast as we can build them,” says Paul Mikesell, cofounder and CEO. “Our customers are mostly high-value crop producers on the East and West Coast, as well as some organic corn and soybean producers. We have sold, but not yet delivered, some in the Midwest.”
Mikesell and key staff have extensive backgrounds in computer vision, machine learning, robotics and other computer-based technologies. Their knowledge of currently available technologies that could be applied to agriculture allowed them to move rapidly from start-up in 2018 to a commercial product 4 years later.
“Everything we use in our laser weeder has a life in another industry,” says Mikesell. “We had to reapply circuits and well-commoditized components for use in a farm field. We had to figure out how to make them rugged. We learned new ways to break things every day. The wind and dust were a real challenge.”
The first prototype was a cart they pushed through a field. They had to ground truth not only the lasers but also the cameras and computers needed to do the job, not to mention the supercomputer that instantly analyzes gathered data and decides which plants to zap.
“We started buying higher and higher-powered lasers to burn the weeds,” recalls Mikesell. “We went from 40-watt lasers to 150 watts.”
Prototypes quickly progressed to the initial product. Their 2022 LaserWeeder Implement is a 20-ft. wide, 3-pt. mounted system that kills up to 99 percent of weed seedlings with sub-millimeter accuracy. It travels at 1 mph, covering 2 acres per hr., 24 hrs. a day. Tracking cameras identify the weeds with the help of LED light bars. Deep learning systems and precision computer vision software used in the onboard supercomputer direct the lasers. The lasers and computer system are powered by a front-mounted, pto-driven generator.
With its 2 1/2-ft. clearance, the system is designed to kill weeds at the seedling stage and continue doing so as needed. Mikesell notes that the type of weed can affect the need for return trips. Grass weeds that spread underground continue to send up shoots, and multi-head weeds like purslane require each flower to be zapped.
“It takes less power and time to kill a weed at the cotyledon stage, but the computer vision module in the control system adapts the time and power to larger weeds,” says Mikesell. “As the crop grows, the cameras can see in and between the foliage. It only takes a 5 mm space for the beam. Once a crop canopies, we don’t have to come back. However, a crop like onions requires more trips through the field.”
Along the way, the company took a step back from an end goal of an autonomous machine. While they have an autonomous design, Mikesell explains that it is not practical at this time.
“We found that with irrigation systems and other equipment in the field, it was much simpler to introduce the LaserWeeder on a tractor with an operator,” he says. “For automation, it needs to be more plugged into a total farm central nervous system.”
Mikesell recommends at least a 120-hp. tractor with a 9,000-lb. lift capacity for the LaserWeeder Implement.
A list price for the system has not been made public. Each unit is sold directly to the customer by the company versus a leasing or service-based program.
“The farmers we talked with prefer to own their equipment,” says Mikesell. “That way, they capture all the benefits from the equipment.”
To provide weed control, the LaserWeeder Implement is constantly collecting data. It can tell the operator what weeds are found, in what percentage, and where the most weed pressure is in the field. It also tracks the health of the crop and its canopy stage. These data points are likely just the beginning.
“We haven’t finished with what we can get with our cameras,” says Mikesell. “We can already spot some disease vectors with our cameras. We are working with different manufacturers on other sensors. Over time we will be adding more.”
Contact: FARM SHOW Followup, Carbon Robotics, 807 Aurora Ave. N, Seattle, Wash. 98109 (ph/text 206-486-4766; www.carbonrobotics.com).
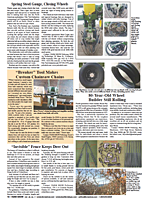
Click here to download page story appeared in.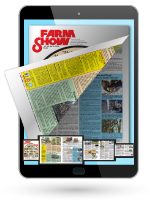
Click here to read entire issue
Zapping Weeds With Lasers SPRAYING New Techniques Carbon Robotics is zapping weeds with lasers saving high-value crop farmers time and money The rear-mounted platforms carry eight laser modules The simultaneously operating laser can kill more than 200 000 weed seedlings per hour while leaving desired seedlings untouched First introduced in February 2022 production is sold out through the end of 2023 “We are shipping them as fast as we can build them ” says Paul Mikesell cofounder and CEO “Our customers are mostly high-value crop producers on the East and West Coast as well as some organic corn and soybean producers We have sold but not yet delivered some in the Midwest ” Mikesell and key staff have extensive backgrounds in computer vision machine learning robotics and other computer-based technologies Their knowledge of currently available technologies that could be applied to agriculture allowed them to move rapidly from start-up in 2018 to a commercial product 4 years later “Everything we use in our laser weeder has a life in another industry ” says Mikesell “We had to reapply circuits and well-commoditized components for use in a farm field We had to figure out how to make them rugged We learned new ways to break things every day The wind and dust were a real challenge ” The first prototype was a cart they pushed through a field They had to ground truth not only the lasers but also the cameras and computers needed to do the job not to mention the supercomputer that instantly analyzes gathered data and decides which plants to zap “We started buying higher and higher-powered lasers to burn the weeds ” recalls Mikesell “We went from 40-watt lasers to 150 watts ” Prototypes quickly progressed to the initial product Their 2022 LaserWeeder Implement is a 20-ft wide 3-pt mounted system that kills up to 99 percent of weed seedlings with sub-millimeter accuracy It travels at 1 mph covering 2 acres per hr 24 hrs a day Tracking cameras identify the weeds with the help of LED light bars Deep learning systems and precision computer vision software used in the onboard supercomputer direct the lasers The lasers and computer system are powered by a front-mounted pto-driven generator With its 2 1/2-ft clearance the system is designed to kill weeds at the seedling stage and continue doing so as needed Mikesell notes that the type of weed can affect the need for return trips Grass weeds that spread underground continue to send up shoots and multi-head weeds like purslane require each flower to be zapped “It takes less power and time to kill a weed at the cotyledon stage but the computer vision module in the control system adapts the time and power to larger weeds ” says Mikesell “As the crop grows the cameras can see in and between the foliage It only takes a 5 mm space for the beam Once a crop canopies we don’t have to come back However a crop like onions requires more trips through the field ” Along the way the company took a step back from an end goal of an autonomous machine While they have an autonomous design Mikesell explains that it is not practical at this time “We found that with irrigation systems and other equipment in the field it was much simpler to introduce the LaserWeeder on a tractor with an operator ” he says “For automation it needs to be more plugged into a total farm central nervous system ” Mikesell recommends at least a 120-hp tractor with a 9 000-lb lift capacity for the LaserWeeder Implement A list price for the system has not been made public Each unit is sold directly to the customer by the company versus a leasing or service-based program “The farmers we talked with prefer to own their equipment ” says Mikesell “That way they capture all the benefits from the equipment ” To provide weed control the LaserWeeder Implement is constantly collecting data It can tell the operator what weeds are found in what percentage and where the most weed pressure is in the field It also tracks the health of the crop and its canopy stage These data points are likely just the beginning “We haven’t finished with what we can get with our cameras ” says Mikesell “We can already spot some disease vectors with our cameras We are working with different manufacturers on other sensors Over time we will be adding more ” Contact: FARM SHOW Followup Carbon Robotics 807 Aurora Ave N Seattle Wash 98109 ph/text 206-486-4766; www carbonrobotics com
To read the rest of this story, download this issue below or click
here to register with your account number.