You have reached your limit of 3 free stories. A story preview is shown instead.
To view more stories
(If your subscription is current,
click here to Login or Register.)
“Stitching” Process Repairs Cracked Cast Iron
A “metal stitching” technique invented in the 1930’s to successfully repair cracked or broken cast metals without welding has been widely used in many industries for over 90 years.
Metalock Engineering in the U.S. and Herculock in Canada use the technique to repair old steam engines, commercial boilers, ind
..........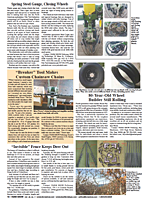
You must sign in, subscribe or renew to see the page.
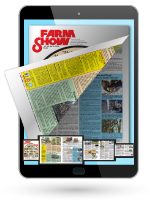
You must sign in, subscribe or renew to see the flip-book
“Stitching” Process Repairs Cracked Cast Iron ENGINES A “metal stitching” technique invented in the 1930’s to successfully repair cracked or broken cast metals without welding has been widely used in many industries for over 90 years Metalock Engineering in the U S and Herculock in Canada use the technique to repair old steam engines commercial boilers industrial equipment ships and oil field equipment Gerald Cyr at Herculock says the cold cast technique known as metal locking repairs a crack without adding extra stress to the part Cyr says the process has been used effectively to repair broken crankcases and other parts on century-old engines The cracked area is thoroughly cleaned and the repair design is determined by magna flux or dye penetrant testing The stitching process requires drilling small holes and adjoining shoulders along the fractured area Metal dowel key strips and lacing bolts are inserted into the holes and peened driven into place with pneumatic tools Peening expands the surface of the cold metal into the area of the fissure and relieves tensile stresses to strain-harden the surface metal The process adds rigidity to the repaired area and creates an extremely strong joint The exposed metal pieces are then ground smooth to the surface revealing only the stitch lines extending into the solid metal adjacent to the crack Cyr says repaired areas have excellent shear load resistance and hydraulic pressure levels of up to 10 000 psi can be achieved The native metal isn’t damaged or distorted because heat isn’t used in the repair Metal locking is an ideal alternative to welding on metals where using heat isn’t possible or recommended Search Google com for “metal stitching cast iron” for more information on the technique Contact: FARM SHOW Followup Metalock Engineering www metalockengineering us or Herculock Ltd herculock@duny ca
To read the rest of this story, download this issue below or click
here to register with your account number.