Field Disc Converted To Roller/Crimper
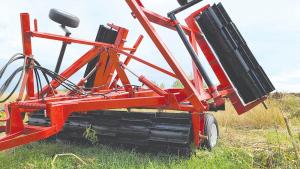 ✖  |
Smaller discs are a dime a dozen, so Michael Bredeson and Ryan Schmid decided to convert one to a roller/crimper for cover crops. The research scientists at Ecdysis Foundation, along with their farmer advisor group, came up with the idea. It was a natural second step for the group after building an inter-row drill for seeding cover crops into established corn.
“We had converted an IH cultivator toolbar to carry row units from an old Haybuster no-till drill,” says Bredesen. “One of the farmers in the group had a couple of Gandy box seed regulators. We slapped them on and made it work. That sparked our interest in building equipment for use with cover crops.”
The farmer/researcher group was interested in working with a roller/crimper for cover crop termination. They felt commercial units were too highly-priced, and no one in the area had one for the group to experiment with.
“We figured our role was to lower the barrier of entry,” says Bredesen. “Farmers in our group are welders and machinists, and they taught us how to do cutting, welding, and plasma welding.”
The team applied for and received a grant from North Central Sustainable Agriculture Research and Education. The grant was for $6,740, the estimated cost of materials.
They started with an International 490 22-ft. disc with a 10-ft. center section and two 6-ft. wings. The disc had been sitting in the wood grove of one of the farmer advisors. Bredesen and Schmid stripped away the gangs.
The first challenge was that the crimping drums were bigger than the disc gangs. The placement of the wings had to be reconfigured, so the drums didn’t catch on the ground when the wings folded down.
“Mike did a lot of measuring,” says Schmid. “We also needed the crimping drums to slightly overlap each other and for the transit wheels to fold up underneath when the wings were folded down.”
“We sketched it out so many times we were sick of it,” says Bredeson. “We used whiteboards and power points trying to understand it. At one point, while debating between straight blades and chevrons, we built a dummy of a roller.”
They used cardboard for the roller drums and bamboo shish kebab sticks for the blades. The sticks extended out the same distance from the drums as the blades would.
“We ran it across the kitchen floor to see what the bounce would be,” recalls Bredesen. “Later, we slapped the cardboard template on the end of the roller drums to see where rows of blades should go.”
“We went with six sets of 23-in. long steel blades on the 11-ft. center drum,” says Schmid. “Each 6-ft., 8-in. wing drum has four sets of slightly offset, 20 3/4-in. blades. Each set of 11 blades overlaps each other by an inch.”
The drums were fabricated from 16-in. O.D. oil pipe found at a salvage yard. The 1/4-in. thick crimper blades extend out from the drum 4 in. Each blade was reinforced by three 3-in. by 1 1/2-in. gussets.
“We were able to use the original hydraulics,” says Schmid. “We did have to replace some hoses.”
The fabrication was done over the winter of 2021/2022. In the spring the roller/crimper was put to the test. It was used by three farmers, one with 10 acres of cereal rye.
“He was very happy with its crimping ability,” says Schmid. “Another farmer used it on a thin stand of rye. It didn’t work as well, which is standard for crimping thin stands. The last one used it on a patch of Canadian thistles at the end of June. It was heavy enough to break the stems.”
No vibration problems were seen, even at up to 9 mph. However, the field tests illustrated that more overlap of the drums was needed. They also needed a little more weight.
“We drilled holes in the drums so we can fill them with water this spring,” says Bredeson.
Overall, the researchers and their farmer advisors are satisfied with the results. While it would have been easier to build a single 11-ft. roller/crimper, one of the goals was an implement that moderate-size farmers would consider.
“We liked this size because implement dealers tell us that any disc under 30 ft. is cheap to buy,” says Schmid. “At the same time, a smaller farmer can look at the plans and make one with a single drum.”
The project was also a success financially. Schmid estimates a commercial roller crimper of the same size would cost from $30,000 to $35,000.
“Ours cost $5,883, $857 under our initial estimate,” says Schmid. “If we can do it with next to no experience and make a functional unit, a lot of farmers could make it even better.”
Contact: FARM SHOW Followup, Ecdysis Foundation, 46958 188th St., Estelline, S.D. 57234 (ryan.schmid@ecdysis.bio; mike.bredeson@ecdysis.bio; www.ecdysis.bio).
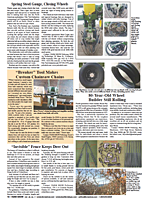
Click here to download page story appeared in.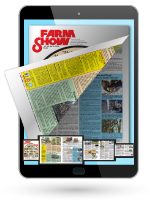
Click here to read entire issue
Field Disc Converted To Roller/Crimper DISKS Smaller discs are a dime a dozen so Michael Bredeson and Ryan Schmid decided to convert one to a roller/crimper for cover crops The research scientists at Ecdysis Foundation along with their farmer advisor group came up with the idea It was a natural second step for the group after building an inter-row drill for seeding cover crops into established corn “We had converted an IH cultivator toolbar to carry row units from an old Haybuster no-till drill ” says Bredesen “One of the farmers in the group had a couple of Gandy box seed regulators We slapped them on and made it work That sparked our interest in building equipment for use with cover crops ” The farmer/researcher group was interested in working with a roller/crimper for cover crop termination They felt commercial units were too highly-priced and no one in the area had one for the group to experiment with “We figured our role was to lower the barrier of entry ” says Bredesen “Farmers in our group are welders and machinists and they taught us how to do cutting welding and plasma welding ” The team applied for and received a grant from North Central Sustainable Agriculture Research and Education The grant was for $6 740 the estimated cost of materials They started with an International 490 22-ft disc with a 10-ft center section and two 6-ft wings The disc had been sitting in the wood grove of one of the farmer advisors Bredesen and Schmid stripped away the gangs The first challenge was that the crimping drums were bigger than the disc gangs The placement of the wings had to be reconfigured so the drums didn’t catch on the ground when the wings folded down “Mike did a lot of measuring ” says Schmid “We also needed the crimping drums to slightly overlap each other and for the transit wheels to fold up underneath when the wings were folded down ” “We sketched it out so many times we were sick of it ” says Bredeson “We used whiteboards and power points trying to understand it At one point while debating between straight blades and chevrons we built a dummy of a roller ” They used cardboard for the roller drums and bamboo shish kebab sticks for the blades The sticks extended out the same distance from the drums as the blades would “We ran it across the kitchen floor to see what the bounce would be ” recalls Bredesen “Later we slapped the cardboard template on the end of the roller drums to see where rows of blades should go ” “We went with six sets of 23-in long steel blades on the 11-ft center drum ” says Schmid “Each 6-ft 8-in wing drum has four sets of slightly offset 20 3/4-in blades Each set of 11 blades overlaps each other by an inch ” The drums were fabricated from 16-in O D oil pipe found at a salvage yard The 1/4-in thick crimper blades extend out from the drum 4 in Each blade was reinforced by three 3-in by 1 1/2-in gussets “We were able to use the original hydraulics ” says Schmid “We did have to replace some hoses ” The fabrication was done over the winter of 2021/2022 In the spring the roller/crimper was put to the test It was used by three farmers one with 10 acres of cereal rye “He was very happy with its crimping ability ” says Schmid “Another farmer used it on a thin stand of rye It didn’t work as well which is standard for crimping thin stands The last one used it on a patch of Canadian thistles at the end of June It was heavy enough to break the stems ” No vibration problems were seen even at up to 9 mph However the field tests illustrated that more overlap of the drums was needed They also needed a little more weight “We drilled holes in the drums so we can fill them with water this spring ” says Bredeson Overall the researchers and their farmer advisors are satisfied with the results While it would have been easier to build a single 11-ft roller/crimper one of the goals was an implement that moderate-size farmers would consider “We liked this size because implement dealers tell us that any disc under 30 ft is cheap to buy ” says Schmid “At the same time a smaller farmer can look at the plans and make one with a single drum ” The project was also a success financially Schmid estimates a commercial roller crimper of the same size would cost from $30 000 to $35 000 “Ours cost $5 883 $857 under our initial estimate ” says Schmid “If we can do it with next to no experience and make a functional unit a lot of farmers could make it even better ” Contact: FARM SHOW Followup Ecdysis Foundation 46958 188th St Estelline S D 57234 ryan schmid@ecdysis bio; mike bredeson@ecdysis bio; www ecdysis bio
To read the rest of this story, download this issue below or click
here to register with your account number.