You have reached your limit of 3 free stories. A story preview is shown instead.
To view more stories
(If your subscription is current,
click here to Login or Register.)
Wood Splitter Runs On Wood Gas
David Boyt makes lots of wood chips sawing up logs, as much as a ton on good days. He also burns about 4 gals. of gasoline. With a ton of wood chips equaling the energy in 120 gals. of gasoline, it made sense to put them to work.
“Running my gasoline engine on wood gas has been on my to-do list for over 40 year
..........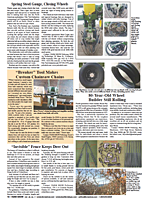
You must sign in, subscribe or renew to see the page.
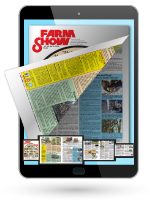
You must sign in, subscribe or renew to see the flip-book
Wood Splitter Runs On Wood Gas ENERGY Wood Gas David Boyt makes lots of wood chips sawing up logs as much as a ton on good days He also burns about 4 gals of gasoline With a ton of wood chips equaling the energy in 120 gals of gasoline it made sense to put them to work “Running my gasoline engine on wood gas has been on my to-do list for over 40 years ” says Boyt “Cars trucks motorcycles tractors barges and even German tanks were converted to run on wood during World War II However after the war most people happily scrapped their wood gasifiers and returned to the convenience of gasoline and diesel ” Boyt notes that when fuel prices skyrocketed in the 1970’s interest in gasifiers flared up Vol 28 No 4 In a belated response the Federal Emergency Management Agency FEMA published a manual Construction of a Simplified Wood Gas Generator for Fueling Internal Combustion Engines in a Petroleum Emergency Boyt used the manual as a basis for his project quickly learning the manual overestimated ease of construction “FEMA claims the gasifier can be built in a couple of days from commonly available scrap with simple tools and no special skills ” says Boyt “That assumes you have 6-in steel pipe 4-in threaded pipe caps and more in your scrap pile “It also assumes you have the skills and tools for airtight brazing stainless steel welding and cutting 1/8-in steel plate ” he adds The manual was for a stratified downdraft design Smoke from burning chunks of wood is pulled down through the fire tube and with the charcoal produces carbon monoxide hydrogen and some methane These gasses are filtered cooled and diverted to the engine to fuel it in place of gasoline An essential element of the plan is that the gasifier be airtight This is vital not only for operation but also for safety A wood gas leak could flare unexpectedly Components included the fire tube a grate the enclosing barrel a 5-gal filter chamber filled with wood chips and a flexible steel hose between the barrel the filter chamber and the engine carburetor Other elements included a cleanout tube at the bottom of the barrel a shaker mechanism to prevent ash buildup in the grate and a blower to initiate downdraft Once completed all that remained was firing it up That was a multi-step process that included adding a bed of charcoal to the grate through the fire tube and oil-soaked crumpled newspaper on top of the charcoal Boyt then dropped a wad of burning paper in Once the fire was established he first added a 6-in layer of pine wood and then filled the fire tube with oak wood chips and started the blower “The first time all I had was smoke ” says Boyt “The second time I oven-dried wood cubes for several hours and once the fire started I paid close attention to the mix of air and wood gas ” He notes that it took trial and error to get the right mix Once he had the engine running smoothly it ran without hesitation His first use of the wood gas was on an engine powering a wood splitter It ran without hesitation Contact: FARM SHOW Followup David Boyt 20632 Parrot Rd Neosho Mo 64850 ph 417-455-2698; dboyt@netins net; www pottershophollow com
To read the rest of this story, download this issue below or click
here to register with your account number.