2023 - Volume #47, Issue #3, Page #04
[ Sample Stories From This Issue | List of All Stories In This Issue | Print this story
| Read this issue]
“No Heat” Crop Dryer
![]() |
“We’ve used the Dry Max technology in the lab to dry alfalfa, protein wet cake and grain,” says Eichhorn. “Grain is the hardest to dry, as the moisture has to leave through the limited space at the germ end. With grass and high moisture materials, the water exits everywhere.”
Grain may indeed be hard to dry, but that’s the market he’s focused on first. According to Eichhorn, RWE is 97 percent efficient compared to 30 percent efficiency with conventional crop drying technologies. Unlike them, RWE doesn’t cost more to dry crops at 30 percent than it does at 20.
“Farmers will be able to harvest grain greener, yet with lower drying costs,” says Eichhorn. “Crops are vulnerable to yield losses of 2 to 4 percent per week when left in the field to dry. A Forcefield grain dryer will capture more of the yield.”
Another advantage is speed of drying. Free water comes out very fast, suggests Eichhorn. “We can dry a 3-ft. grain wall, while conventional dryers can only do 8 to 10 in.,” he says. “Our cost to dry will be much less than half that of a propane gas dryer, and the price won’t increase during drying season as propane does. We use electricity, and those rates don’t change.”
The Forcefield technology may be fast, but it’s also gentle. The radio waves pass through the outer shell to target the highest moisture first. Instead of drying from the outside in with high heat, moisture is released from the inside out. Nutrients and crop integrity, as well as volatiles like taste and smell, are preserved, while mold, mildew, insects and other problem organisms are killed. Crops intended for seed also benefit from the gentle system, with germination rates of 98+ percent.
The Dry Max system is designed to be modular for easy transport. The Forcefield technology can be applied to batch dryers and tower dryers, as well as horizontal dryers. It can be scaled up for whatever volume is needed on a bushel per hour or tons per hour basis.
Eichhorn acknowledges that initial units will be more expensive than conventional dryers. As numbers increase, economies of scale will lower prices. In the meantime, he’s confident the lower cost of drying and other advantages of a Dry Max system will justify the investment.
“We plan to begin production next year and are looking for our first 100 customers for the 2024 crop drying season.”
Once the initial basic unit is in production, Eichhorn has add-on units planned. “Our add-ons will allow farmers to use the Dry Max Forcefield system to dry alfalfa, manure, waste products and other materials,” says Eichhorn.
Contact: FARM SHOW Followup, Dry Max Solutions, Eden Prairie, Minn. 55344 (ph 612-770-4189; info@drymaxsolutions.com; www.drymaxsolutions.com).
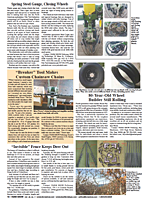
Click here to download page story appeared in.
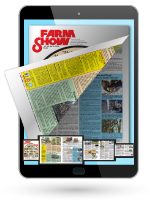
Click here to read entire issue
To read the rest of this story, download this issue below or click here to register with your account number.