You have reached your limit of 3 free stories. A story preview is shown instead.
To view more stories
(If your subscription is current,
click here to Login or Register.)
Field Roller Made From Anhydrous Tanks
“My dad Brian and I looked at the cost of buying a new or used land roller last winter and decided it was way too expensive, so we decided to build one ourselves if we could find the right toolbar,” says Brad Farmer. “Building tools or smaller equipment, welding and fabrication has been a big part of my life growing up
..........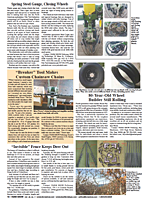
You must sign in, subscribe or renew to see the page.
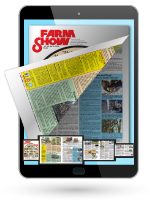
You must sign in, subscribe or renew to see the flip-book
Field Roller Made From Anhydrous Tanks MISCELLANEOUS EQUIPMENT Miscellaneous “My dad Brian and I looked at the cost of buying a new or used land roller last winter and decided it was way too expensive so we decided to build one ourselves if we could find the right toolbar ” says Brad Farmer “Building tools or smaller equipment welding and fabrication has been a big part of my life growing up so taking on this large of a project wasn’t a problem ” Farmer says his design ideas came from the 14-ft used roller his dad bought at an auction several years ago “The owner built it out of an old LP tank and used 10-20 truck tires to transport it We use it every year rolling fields after seeding small grain and it works great so we thought why not make a large one using the same concept?” Farmer turned to an internet marketplace website to locate a toolbar that he could use to transport his roller Just 20 minutes from his shop he found a used Deere 7000 16-row planter toolbar without any row units “It was the perfect carrier and all I needed to do was remove hardware and bracing that held the markers fertilizer pump and coulter mounts ” Farmer says To make the rollers he bought two used anhydrous tanks from a local scrap yard and another from a local farmer He removed the ends of all three tanks with his plasma cutter removed the filler pipe fittings and then welded plate steel over the openings to keep dirt from getting inside the rollers “I wanted the end pieces to be very precise so I had a local welding shop with a computer plasma cut them to size ” Farmer says “Each one is 41 5/16 in in diameter 3/8 in thick with a 2-in by 7/16-in solid shaft for the axle Each roller weighs about 2 700 lbs is 14 1/2 ft long and 42 in in diameter ” Farmer mounted the wing rollers on the bar using 5/8-in thick flat steel brackets He extended the ends of both wings with 7 by 7-in by 3/8-in thick square tubing “It was very important to do this so that each side drum would have at least one foot of overlap to the rear drum and drop about 7 in below the toolbar so I could raise the wheels in the field ” Farmer says The wing rollers are mounted 36 in behind the bar with 5/8-in brackets and gusseted framework The rear roller is built onto a subframe made of 7 by 7-in square tubing that extends about 5 ft behind the main toolbar Hydraulic cylinders on the main frame fold the two wings forward and to the center where they lock in place with a separate cylinder for road travel Farmer uses the 2-pt hitch on his tractor to raise the front of the roller Two cylinders raise the back wheels providing 14 in of road clearance A manual safety lock secures the wheel’s cylinders The entire 42-ft roller folds to 15 ft wide for road travel slightly larger than the width of the center roller Farmer designed the hydraulics with one remote and an electric control box so he can fold and unfold the roller from the tractor cab One solenoid handles the transport wheels another folds and closes the wings and a third locks the wings “I plan to streamline this for next year by plumbing the remotes direct and eliminating the solenoids ” Farmer says For an investment of about $10 000 and his time for labor Farmer says that he and his dad now have a custom-built roller that’s just as good as a new one for about a third of the cost or less Contact: FARM SHOW Followup Brad Farmer 3596 Trophy Ave Osage Iowa 50461 farmer3596@gmail com
To read the rest of this story, download this issue below or click
here to register with your account number.