You have reached your limit of 3 free stories. A story preview is shown instead.
To view more stories
(If your subscription is current,
click here to Login or Register.)
Combine Turned Into Big Bale Handler
A self-propelled "clamp loader" built from an old Massey Ferguson 510 combine lets Mark Kuehl, Ashton, Idaho, carry two big square bales at a time.
Kuehl calls his unconventional machine the "Beast". He built it for about $8,000 including the cost of the loader.
He paid $1,600 for the combine, which was equ
..........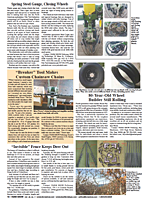
You must sign in, subscribe or renew to see the page.
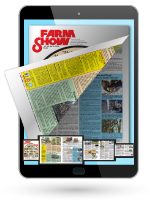
You must sign in, subscribe or renew to see the flip-book
Combine Turned Into Big Bale Handler COMBINES Conversions 20-3-40 A self-propelled "clamp loader" built from an old Massey Ferguson 510 combine lets Mark Kuehl, Ashton, Idaho, carry two big square bales at a time.
Kuehl calls his unconventional machine the "Beast". He built it for about $8,000 including the cost of the loader.
He paid $1,600 for the combine, which was equipped with a 327 cu. in. gas engine and 3-speed hydrostatic belt-driven trans-mission. He stripped the combine down, keeping the engine, operator platform, and running gear. He used 4 by 8 steel tubing to build a new frame and fitted it with a cab off a 1980 Gleaner L combine. He also equipped it with a Deere 260 loader. In or-der to direct-drive the hydrostatic transmission, he had to have a special adapter plate made to fit the flywheel. By direct-coupling the hydrostatic transmission directly to the flywheel he was able to keep the engine in line with the cab without having to turn it sideways.
He used steel tubing to build a U-shaped bale clamp which has one telescopic arm that extends out sideways via a 3 by 24-in. hydraulic cylinder.
"Considering that a used 80 hp tractor and loader sells for $18,000 to $20,000 it saved me at least $10,000," says Kuehl, who credits his mechanic friends Matt Black, John Scafe, Joe Pilgrim, and Duncan Bollinger for doing most of the mechanical work. "I use it to load bales onto a trailer in summer and to feed them out in winter. I got the idea when I switched from making small square bales to big square bales. I didn't want to use a diesel loader tractor in the winter to feed cattle.
"My New Holland D1000 baler makes bales that are 2 ft. high, 3 ft. wide, and 7 ft. long and weigh about 500 lbs. each. As the bales come out of the baler they make a 1/4 turn and land on their side with the strings off the ground. I stack the bales the same way. When I retrieve them for feeding I re-move the strings, then pick up two bales at a time and drop them in a feeder. I also make some 1-ton bales. When necessary, I can remove the clamp and replace it with a bale spear. I can also use a loader bucket for other work.
"The loader is powered by the header hydraulics and the bale clamp cylinder by an auxiliary valve. I use foot pedals to raise and lower the arms, tilt the clamp, and move the clamp in or out, leaving my hands free for steering. The hydrostatic drive eliminates clutching or shifting for forward or reverse travel. The engine on back acts as a counterweight to the loader and also allows a clear view ahead of me. By taking out four bolts I can remove the hood and lift the engine and transmission out for repairs."
Contact: FARM SHOW Followup, Mark Kuehl, 1314 N. 4200 E., Ashton, Idaho 83420 (ph 208 652-3740).
To read the rest of this story, download this issue below or click
here to register with your account number.