2023 - Volume #47, Issue #6, Page #25
[ Sample Stories From This Issue | List of All Stories In This Issue | Print this story
| Read this issue]
He Built His Own Grapple Fork
![]() |
“I’m not one to make drawings or design formal plans as I tend to change things too much on the go,” Angus says. “I looked online and at new grapples to figure out how to build mine.”
He decided to go with a straight bottom rather than curved like many manufactured grapples, to keep it simple and workable.
The long-time welder and part-time farmer bought stock metal for the project. He used 3/8-in. plate steel for the nine middle bottom teeth and 1/2-in. steel for the two outer teeth. For the main frame and cross braces, he chose 2 1/2-in. square tubing. To create the curved top grapple fingers, he ordered 1/2-in. replacement box scraper rippers and welded them in place. A hydraulic hose to the rear of the tractor operates the hydraulic cylinder for opening and closing the fork.
“It opens up almost vertically and gets a big bite,” Angus says. “I hauled out over 50 pine trees from the woods, some up to 1,000 lbs. The grapple fork also has a variety of other uses like picking up and moving brush piles or handling straw bales.”
Angus estimates he spent about $1,200 on the grapple fork materials, not counting the hydraulic ram which he already had.
Contact: FARM SHOW Followup, George Angus, 6362 Bunkerhill South Road, Butler, Ohio 44822 (ph 419-564-0524; peteangus9@aol.com).
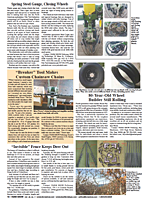
Click here to download page story appeared in.
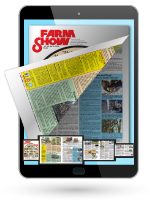
Click here to read entire issue
To read the rest of this story, download this issue below or click here to register with your account number.