You have reached your limit of 3 free stories. A story preview is shown instead.
To view more stories
(If your subscription is current,
click here to Login or Register.)
He Built A Working Steam Train From Wood
Harold Manwaring spent more than 7 years working as a fitter and turner for the railroad, but his love of trains stayed with him long after he left his job. As he drove trucks and heavy equipment in a new career, he thought about how to build a wooden locomotive. At age 60 in 1997, he began wood crafting by learning to
..........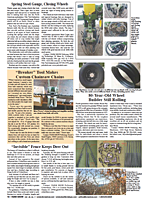
You must sign in, subscribe or renew to see the page.
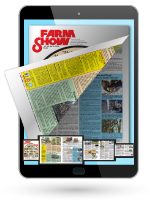
You must sign in, subscribe or renew to see the flip-book
He Built A Working Steam Train From Wood AG WORLD Harold Manwaring spent more than 7 years working as a fitter and turner for the railroad but his love of trains stayed with him long after he left his job As he drove trucks and heavy equipment in a new career he thought about how to build a wooden locomotive At age 60 in 1997 he began wood crafting by learning to use a woodworker’s lathe then built several jigs for holding and drilling wheels and journals Manwaring says the skills he gained on numerous bowls led him to tackle a working locomotive Friends told him he couldn’t build one that ran on compressed air but he proved them wrong The result is a 560-piece wooden masterpiece depicting a 4-4-0 steam locomotive Made with nine different kinds of wood the project took him about 3 years to make The completed locomotive and tender rests on a 3-ft long platform Manwaring says he gave the functional working parts just enough lubrication they’d operate without sticking The loco produces steam and its wheels turn freely because they’re raised slightly above the wooden track Compressed air is fed into a small stainless receiver in the firebox at 15 psi The lines cylinders and pistons are all made of wood The cylinders have a 1 1/8 in bore and 1 1/2 in stroke Pistons have wooden rings just 1/16 in thick made like conventional automobile models Manwaring says the engine runs effortlessly with the steam exhaust emitted through the stack with a calm “chuffing” sound Manwaring modeled his masterpiece from a 4 1/2-in picture of a Philadelphia Germantown and Morristown Railroad locomotive built in 1837 He used a magnifying glass to judge and document the part sizes he needed The cream-colored wood is from street-cut trees in the town of Wagga Wagga Desert ash was used for the cabin boiler and many working components Other woods include red river gum olive wood jarrah wood Australian red cedar Queensland maple and Osage orange Some parts are held together with tiny metal pieces although most are held with two-part epoxy and PVA woodworker’s glue Manwaring made the steel tube inside the engine body from scraps of car muffler tube Valves were made from old water tap spindles Ball bearings and springs came from a tiny electric motor Even the whistle works emitting a shrill tune using 2 to 3 lbs of air Manwaring says the whole project was quite tedious and also very satisfying “The engine worked the first time I turned on the air and with that I stopped and celebrated with a beer ” Contact: FARM SHOW Followup Harold Manwaring New South Wales Australia
To read the rest of this story, download this issue below or click
here to register with your account number.