You have reached your limit of 3 free stories. A story preview is shown instead.
To view more stories
(If your subscription is current,
click here to Login or Register.)
His Hobby Is Backyard Steel Making
Richard Furrer has a pile of iron ore in his backyard, waiting to be smelted into steel and made into knives and more. Furrer has been practicing the blacksmith trade and art for 33 years. He usually works with bronze, aluminum, stainless steel, and titanium. In addition to architectural work, he also forges knives and
..........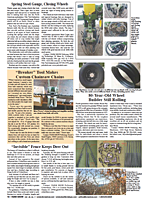
You must sign in, subscribe or renew to see the page.
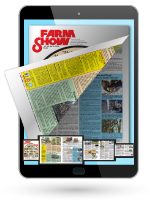
You must sign in, subscribe or renew to see the flip-book
His Hobby Is Backyard Steel Making FARM SHOP Miscellaneous Richard Furrer has a pile of iron ore in his backyard waiting to be smelted into steel and made into knives and more Furrer has been practicing the blacksmith trade and art for 33 years He usually works with bronze aluminum stainless steel and titanium In addition to architectural work he also forges knives and swords Many of the latter are made from his backyard ore pile He learned the process the hard way pre-YouTube and internet postings “My first smelt was with a University of Wisconsin Madison professor of archeological studies ” recalls Furrer “He was trying to recreate the basic chemistry and physics of ancient steel making It was a mixed bag of success and failure but I never gave up on it ” Furrer continued to refine the process improving the outcome He credits the internet for expanding on information once found only in archeological texts However he gives the most credit to trial and error The basic process involves building the furnace a stack of bricks or even mud walls Furrer uses an insulated blanket to create a taller stack without the increased weight of more bricks A tap allows waste to flow out of the furnace while the bloom of steel settles in the bottom One of the keys to success is the quality of iron Iron ore in places like Great Britain is very poor quality while ore in Australia can be 90 percent pure iron Furrer prefers bog or lake iron concentrated by bacteria once found in some lakes It had one molecule of oxygen and one of iron The bog iron would be found in clumps the size of a baseball or softball Perhaps due to environmental reasons the bacteria are no longer found Furrer’s pile of ore is from mine tailings from northern Minnesota Once charcoal and ore are introduced and the fire starts the results are a matter of getting the correct mix of air fuel and ore “You can always expect something to go slightly wrong ” he says “However a few months ago I did a smelt and we got a 30 percent yield which is almost perfect for bloomery steel ” For Furrer an optimal effort would produce 15 lbs of bloomery from 50 lbs of ore and charcoal After working the bloomery over in a forge the result would be 5 to 6 lbs of finished product ” Furrer uses his ore for himself and in the classes he teaches Classes are multi-day affairs and small in size Prices vary A 5-day class for a group of four can cost $1 000 each “We had one class with eight students and we built two furnaces one in the European style and one in the Japanese style ” recalls Furrer “Both furnaces yielded bloomery that we melted together and worked in the forge Each student was able to make a knife blade from the steel ” While some classes he teaches involve producing a knife or other object that often isn’t what attracts students “Some just want the experience ” he says “Others want to make steel While they could just experiment a class can take years off the learning curve ” Contact: FARM SHOW Followup Door County Forgeworks 3179 May Rd Sturgeon Bay Wis 54235 ph 608-852-5226; www doorcountyforgeworks com
To read the rest of this story, download this issue below or click
here to register with your account number.