You have reached your limit of 3 free stories. A story preview is shown instead.
To view more stories
(If your subscription is current,
click here to Login or Register.)
Shop-Built Rolling Anvil Rail Table
Jerome Behm had the perfect anvil for popping rivets in and out of a sickle bar. To make the long anvil, he mounted a 10 ft. length of railroad rail topside down on stationary legs. A second set of legs with caster wheels is lowered to raise the anvil/rail table for moving about the shop.
“I made it back when si
..........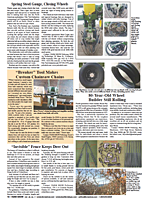
You must sign in, subscribe or renew to see the page.
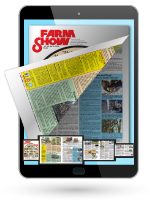
You must sign in, subscribe or renew to see the flip-book
Shop-Built Rolling Anvil Rail Table FARM SHOP Maintenance Jerome Behm had the perfect anvil for popping rivets in and out of a sickle bar To make the long anvil he mounted a 10 ft length of railroad rail topside down on stationary legs A second set of legs with caster wheels is lowered to raise the anvil/rail table for moving about the shop “I made it back when sickle bars still used rivets to fasten the blades to the bar ” says Behm “Sickle bolts replaced rivets so I don’t use the table for that anymore but it’s still handy as a mobile anvil I can easily roll it around on the shop’s concrete floor ” The stationary legs are 3-in steel round stock cut at 30-degree angles welded to 6-in sq plates for bases Matching plates welded to the tops of the legs are bolted together below and through the rail sandwiching it between them Making the unit mobile required mounting a second set of legs with casters between the stationary legs and connected to them and the rail A winch and cables running through a system of pulleys force the legs on casters down while lifting the rail table up The winch is mounted just inside the pairs of legs at one end of the rail Its cable connects through a ferrule and eyelet to a pair of lift cables at the far set of legs At each end of the rail short about 10-in lengths of round stock connect both sets of stationary legs to square frames that house the castor wheel legs The frames stabilize the caster wheel legs while allowing them to move up and down Square tubing mounted to the top of each set of caster wheel legs forms an upside-down T over the legs The Ts vertical leg connects to the rail with a piston that accommodates the leg’s movement A tab to one side of the vertical leg anchors an eyelet for the cable system A spring mounted between the stabilizing frame and a tab on the other side raises the legs when the winch is not in use A second vertical post extends from the stationary leg frame to the underside of the rail A brace extends at a 45-degree angle from it to the rail One lift cable at the far set of legs travels through a pulley in the vertical post brace to a second pulley above it From there it travels back under the rail to a pulley at the matching vertical post brace on the near set of legs It then travels down to the stabilizing frame on those legs The second cable also travels through a pulley on the post brace and down to a pulley on the stabilizing frame of the far set of legs In both cases the cables travel up to the eyelets near the top of the upside-down T connected to the caster wheel legs When Behm turns the winch handle and the cable tightens the caster legs lower and the rail framework rises Once the anvil/rail table has been moved to the desired spot Behm reverses the process Getting the spacing and placement of cables and pulleys correct took Behm several years “I’ve always liked fabrication and metalwork ” he says “While no longer needed for sickle bar work it’s solid and heavy still useful for shop work ” Contact: FARM SHOW Followup Jerome Behm 13500 19th Ave NW Burlington N D 58722 ph 701-833-2220
To read the rest of this story, download this issue below or click
here to register with your account number.