You have reached your limit of 3 free stories. A story preview is shown instead.
To view more stories
(If your subscription is current,
click here to Login or Register.)
Water-Powered Mill Still Going Strong
After nearly a century and a half, Schech’s Mill is still milling corn, wheat, buckwheat, and more. Turbines in the water flowing from the 1/2-mile-long reservoir power the 48-in. dia. 1,000-lb. quartz millstones brought from France in 1876. The historic mill once produced Schech’s Best Flour for local stores. It can s
..........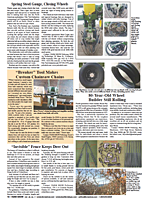
You must sign in, subscribe or renew to see the page.
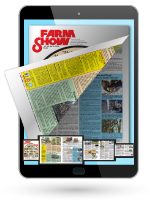
You must sign in, subscribe or renew to see the flip-book
Water-Powered Mill Still Going Strong BUILDINGS Miscellaneous After nearly a century and a half Schech’s Mill is still milling corn wheat buckwheat and more Turbines in the water flowing from the 1/2-mile-long reservoir power the 48-in dia 1 000-lb quartz millstones brought from France in 1876 The historic mill once produced Schech’s Best Flour for local stores It can still grind flour and corn meal animal and bird feed ground corncob bedding for animals and ground grain for a local farmer-owned distillery “We have three original turbines and a newer one purchased in 1924 using the 16 000 gal per min water flow from the mill pond ” says Edward Krugmire mill owner and operator “It’s the last original water-powered mill in Minnesota In addition to grinding grains we offer tours every weekend from late May to late October so people can see how it works ” Krugmire’s great-grandfather Michael Schech purchased the mill from its founder John Blinn in 1887 Over the years it passed down to Michael’s son Edward and Edward’s daughter and husband Eleanor and Ivan Krugmire in 1946 Schech’s Mill was nominated for the National Registry of Historic Places in 1977 At the time it was the only mill in the state to contain unchanged operable milling equipment with original stone Krugmire describes the mill as a non-profit but without official non-profit status That means it’s ineligible for state or federal historic grants to help with upkeep He’s responsible for maintaining the 125-ft wide dam that produces the mill’s 10-ft 3-in water drop and the mill itself It’s the water drop that drives the turbines to power the grain cleaning system corn sheller burr mill millstones sifters and more “Our biggest problem is flooding and the damage it causes to the dam ” says Krugmire “Beyond that an ongoing problem in the winter is water bubbling up and freezing the gears ” One of the turbines drives a belt while the others drive gear systems Krugmire notes that the belt drive requires more maintenance; however the water-powered system is relatively straightforward Belts need to be replaced and millstones need to be dressed Dressing a millstone restores the grooves in the surface ground down by the grain over time Krugmire uses a right-angle grinder with thin beveled diamond wheels “Some of the grooves are less than 1/16 in wide ” marvels Krugmire “I have no idea how they made them in the 1800s ” Krugmire is proud of the mill and his family’s heritage He especially enjoys visitors who appreciate the mill’s history and mechanics “They ask questions and we have great discussions ” he says Krugmire also serves as an unpaid consultant to many individuals and organizations working with old mills “I have connections with people at other mills and those who can help with problems ” he says “I know where to get screening belts and other parts Groups who want to display a historically accurate mill will send someone here to copy parts so theirs looks more authentic ” Krugmire also sells sifting screens for home millers “With a couple of different-sized screens you can remove the bran from flour and make cornmeal ” he says “I make frames for the stainless-steel screening ” He adds “But even with the screens you can’t get grain as fine as my large stones do ” Contact: FARM SHOW Followup Schech’s Mill W Beaver Rd Caledonia Minn 55921 ph 507-896-3481 or 651-245-5566; www schechsmill com
To read the rest of this story, download this issue below or click
here to register with your account number.