1988 - Volume #12, Issue #3, Page #04
[ Sample Stories From This Issue | List of All Stories In This Issue | Print this story
| Read this issue]
Rail Car Loading System
Eight farmers near Chancellor, Alberta, have teamed up to purchase a "Hydra-Swing" auger system that lets them load their own railroad cars with wheat, barley and canola - and save $3 to $6 per ton over elevator chargesAt the heart of the system is a 65 ft. long, 19 in. dia. auger. Driven by a 30 hp electric motor, it's balanced on a 360 degree pivoting saddle located at the end of a 20 ft. long swing arm. The arm also pivots 360 degrees at its center stanchion, which is bolted to a deeply embedded concrete base. A hydraulic cylinder raises and lowers the arm at the touch of a button.
A nearby shed contains controls for the auger and serves as an office. A load cell located under the auger saddle transmits weight to a computer and digital readout mounted in the office, and gives the weight of all grain moving through the auger to within 1% accuracy.
The system also includes a 3,300 bu. surge bin, holding slightly more than one carload of grain.
The eight farmers teamed up to save on elevator charges, which were running $6.25 to $9.25 perton. They became partners with Palliser Grain, a company with lots of experience with producer loaded cars and which also has a grain license. Palliser negotiated the lease with the railroad and administers the shipments.
Since last September, over 40 cars have been shipped through the farmers' track loading system. They hope to self-load 100 to 150 cars per year.
"Canadian Pacific Railway `spots' up to five cars at a time and we have 72 hours to
fill them," explains group member Murray Christensen, Standard, Alberta. "We have to be able to fill the surge bins from trucks, to load cars directly from the surge bin and to load cars directly from trucks.
"Using an ordinary wheeled auger is just not convenient enough for the kind of tonnage we're loading. With this system, the only manual labor is picking up the end of the auger and swinging it into position. We don't have to wrestle with augers as we move them from car to car or compartment to compartment."
From storage, the farmers can fill a car in less than an hour. They can unload a truck in 5 or 6 minutes.
"The surge bin is filled only when we're cramped for time," notes Christensen. "For example, if one farmer needs to load three cars in 72 hours, he won't have enough time if he lives some distance from, the track. Filling the surge bin buys him time."
A 500 watt sodium high pressure flood light is located so that cars can be loaded at night.
Cost of the Chancellor system, fully in-stalled - including all electrical work, with all the options and including the surge bin - was $53,000. "Farmers can start a system for as little as $4,700 by buying the swing arm and mounting their own auger on it," says Ellwood Sawby, owner of Skyway Grain Systems, which designed and in-stalled the system.
For more information, contact FARM SHOW Followup, Skyway Grain Systems, Inc., Box 3414, Airdrie, Alb., Canada T4B 2B6 (ph 403 948-7810).
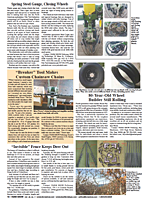
Click here to download page story appeared in.
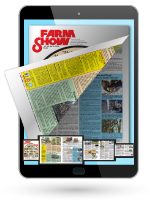
Click here to read entire issue
To read the rest of this story, download this issue below or click here to register with your account number.