2024 - Volume #48, Issue #6, Page #09
[ Sample Stories From This Issue | List of All Stories In This Issue | Print this story
| Read this issue]
Concrete Floor Coating Made To Last
![]() |
“We’ve been doing Duralast polyaspartic coatings for 2 years, and the results have been excellent,” says Bennie Miller, North Country Concrete Coatings. “Polyaspartic coatings are five times stronger than epoxy and come with a 15-year warranty against chipping or peeling.”
Miller warns that studded tires will wear through the surface faster, but with normal traffic, the coating will last the full 15 years. The UV-stable coating will maintain a new look, stand up better to salt, oil and chemical spills and produce a 100 percent antibacterial surface.
“There is nothing wrong with epoxy in some spots, but in my opinion, it doesn’t belong in high-traffic areas like garages,” says Miller. “Customers tell me they’ve put epoxy down, and in a few years or even months, they see it isn’t holding up.”
Polyaspartic coatings have been used on everything from bridges and piers to railcar exteriors and ocean-going barges and ships. They’re non-yellowing and don’t fade or peel with sun exposure. They also have a wide temperature tolerance of -30 degrees to 140 degrees.
Miller points out that epoxy simply bonds to the surface of a concrete floor. Polyaspartic coverings include a polyurea base coat that soaks into the concrete surface. Vinyl flakes are tossed on to give the preferred color before the rubbery base coat dries. Once it has dried, excess flakes are scraped off, and the final polyaspartic coating is rolled down.
“It grabs onto the rough surface of embedded flakes,” says Miller.
The downside of polyaspartic coating is that it’s a more expensive process. It isn’t recommended for concrete floors that give off moisture as they can lose their bond. It also has to be applied quickly.
On the upside, a polyaspartic coating cures five times faster than epoxy. As a result, a job can often be completed in a single day. It has low VOC and odor from outgassing.
Miller stresses that a key element of laying down a polyaspartic coating is properly preparing the concrete floor. “We grind the concrete surface and vacuum it to open up the pores of the concrete,” he says. “This allows the polyurea base coat to soak into the pores,” says Miller.
Miller received training in proper application technique from his distributor, Steve Schmucker, Duralast Concrete Coatings. Schmucker has dealers throughout much of the Midwest, but as far east as New York and as far west as Montana.
Schmucker encourages FARM SHOW readers interested in becoming installers to give him a call. “We’re always looking for dealers and emphasize the support we provide,” he says. “We bring our dealers in for training and then again annually for updates and to address any issues they’ve had. We want our installers educated and well-trained.”
Contact: FARM SHOW Followup, North Country Concrete Coatings, 373 70th Rd., Burke, N.Y. 12917 (ph 518-483-0727; www.northcountryconcretecoatings.com) or Duralast Concrete Coatings, 19427 Notestine Rd., Woodburn, Ind. 46797 (ph 260-341-5640).
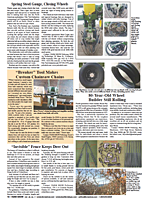
Click here to download page story appeared in.
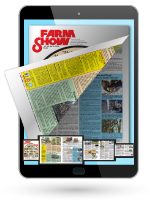
Click here to read entire issue
To read the rest of this story, download this issue below or click here to register with your account number.