Press Upgrades Keep Cider Flowing
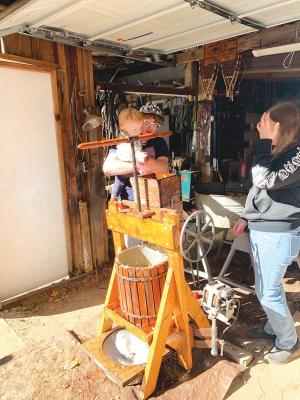 ✖  |
A 40-year-old Garden Way cider press has seen its share of upgrades. Norman Sieting bought it as a kit and has been improving it ever since. The kit included the pressing drum and the hardware. Sieting supplied the wood and assembly. It didn’t take long before he saw a needed change. When he lowered the press plate, it would hit the grinder.
“The grinder was bolted to the back of the cider press frame,” recalls Sieting. “I remounted it so I could remove two wing nuts and take it off. It got it out of the way and made it easy to clean.”
He turned the hand crank on the apple crusher for several years before deciding it was too much work. He decided to motorize it.
“I put a bronze bearing and a pulley on the shaft and supported the bearing by mounting it to the grinder,” says Sieting. “Mounting the pulley next to the bearing kept all the pressure on the bearing. Then I ran a belt to a pulley on a motor from my wife’s first washing machine.”
As usual with Sieting, who has had multiple stories in FARM SHOW, it wasn’t quite that simple. The motor was mounted to a flat plate, which was in turn mounted to a short length of pipe. The pipe rides vertically in a slightly larger pipe that is mounted to the press frame and held in place with a set screw.
“I can slide the pipe attached to the motor down to put tension on the belt or up to remove the belt,” says Sieting.
Motorizing the crusher led to adding a 6-in. extension to the grinder’s hopper. Apple fragments flew out of the 5 by 6-in. hopper as apples hit the faster rotating crushing teeth. The faster crushing speeds also concerned Carol, Sieting’s wife.
“We have a lot of kids come to see the cider press work,” says Carol. “The hopper wasn’t very high, and I worried about kids’ fingers getting too close to the grinder. The hopper extension was a good change.”
While the frame and main components are unchanged, pressing out hundreds, if not thousands, of gallons of cider has had an effect. “The bottom of the pressing pan was curling in with the pressure, so I put a 1 1/2-in. steel band around the bottom to reinforce it,” says Sieting. “I also added wire mesh strainers to the process.”
Initially, Sieting and his wife used cheesecloth to strain the cider. At the time, Sieting worked for a company that made wire mesh filters for aircraft. He decided to line the pressing tub with No. 40 mesh and used a slightly smaller one for the final screening.
“I made a cone-shaped screen to set in a dishpan underneath the pressing pan,” says Sieting. “It keeps out any impurities or small bits of apple. We know it’s clean when we pour the cider into jugs.”
Contact: FARM SHOW Followup, Norman Sieting, 6112 Walker Rd. NW, Rapid City, Mich. 49676 (ph 231-564-1031; normansieting@gmail.com).
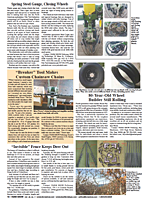
Click here to download page story appeared in.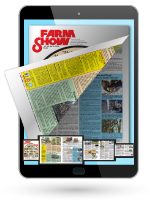
Click here to read entire issue
Press Upgrades Keep Cider Flowing FARM HOME Food A 40-year-old Garden Way cider press has seen its share of upgrades Norman Sieting bought it as a kit and has been improving it ever since The kit included the pressing drum and the hardware Sieting supplied the wood and assembly It didn’t take long before he saw a needed change When he lowered the press plate it would hit the grinder “The grinder was bolted to the back of the cider press frame ” recalls Sieting “I remounted it so I could remove two wing nuts and take it off It got it out of the way and made it easy to clean ” He turned the hand crank on the apple crusher for several years before deciding it was too much work He decided to motorize it “I put a bronze bearing and a pulley on the shaft and supported the bearing by mounting it to the grinder ” says Sieting “Mounting the pulley next to the bearing kept all the pressure on the bearing Then I ran a belt to a pulley on a motor from my wife’s first washing machine ” As usual with Sieting who has had multiple stories in FARM SHOW it wasn’t quite that simple The motor was mounted to a flat plate which was in turn mounted to a short length of pipe The pipe rides vertically in a slightly larger pipe that is mounted to the press frame and held in place with a set screw “I can slide the pipe attached to the motor down to put tension on the belt or up to remove the belt ” says Sieting Motorizing the crusher led to adding a 6-in extension to the grinder’s hopper Apple fragments flew out of the 5 by 6-in hopper as apples hit the faster rotating crushing teeth The faster crushing speeds also concerned Carol Sieting’s wife “We have a lot of kids come to see the cider press work ” says Carol “The hopper wasn’t very high and I worried about kids’ fingers getting too close to the grinder The hopper extension was a good change ” While the frame and main components are unchanged pressing out hundreds if not thousands of gallons of cider has had an effect “The bottom of the pressing pan was curling in with the pressure so I put a 1 1/2-in steel band around the bottom to reinforce it ” says Sieting “I also added wire mesh strainers to the process ” Initially Sieting and his wife used cheesecloth to strain the cider At the time Sieting worked for a company that made wire mesh filters for aircraft He decided to line the pressing tub with No 40 mesh and used a slightly smaller one for the final screening “I made a cone-shaped screen to set in a dishpan underneath the pressing pan ” says Sieting “It keeps out any impurities or small bits of apple We know it’s clean when we pour the cider into jugs ” Contact: FARM SHOW Followup Norman Sieting 6112 Walker Rd NW Rapid City Mich 49676 ph 231-564-1031; normansieting@gmail com
To read the rest of this story, download this issue below or click
here to register with your account number.