You have reached your limit of 3 free stories. A story preview is shown instead.
To view more stories
(If your subscription is current,
click here to Login or Register.)
They Make Custom Apple Harvesters
When British demand for cider skyrocketed in the 1990s and again in 2008, apple growers responded by planting tens of thousands of new trees. Matthew Barnett’s family orchard grew from 34 acres to 90 today. Barnett and his brother Russell responded by building ever-larger harvesters, first for their family and then for
..........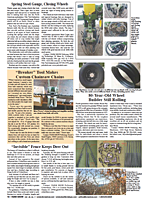
You must sign in, subscribe or renew to see the page.
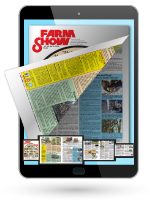
You must sign in, subscribe or renew to see the flip-book
They Make Custom Apple Harvesters When British demand for cider skyrocketed in the 1990s and again in 2008 apple growers responded by planting tens of thousands of new trees Matthew Barnett’s family orchard grew from 34 acres to 90 today Barnett and his brother Russell responded by building ever-larger harvesters first for their family and then for others as MRB Engineering They also designed and built an RTK-guided tractor-mounted machine to plant up to 6 000 trees daily Terry Richardson detailed their efforts in a recent issue of Classic Tractor He describes how MRB repurposes components from self-propelled sprayers potato harvesters and more These are then married with enhanced hydraulics custom-designed chassis and unloading systems loosely based on sugar beet harvesters In a single generation the Barnetts progressed from hand-picking and a 5-hp walk behind to 95 and 110-hp 4-WD 4-wheel steer hydrostatic drive power units The walk behind collected apples in baskets dumped into crates by hand MRB harvesters follow an MRB-designed tree shaker with a gentle grip through the orchard A front-mounted V-shaped paddle system on the tractor-mounted shaker windrows already fallen apples to each side of the row The MRB-designed header directs fruit to elevators that load the mounted hopper The harvester can collect up to 150 tons of apples per day When the hopper is full unloading elevators reach up and over bulk trailers to unload 4 1/2 tons of apples per minute Amazingly they do so gently with minimal damage Space is at a premium in tight orchard row spacing To make room for harvester hoppers the Barnetts relocated the engines on the power units from longitudinal to transverse and lowered the cab This also placed the operator closer to the ground and with a better view of the header A key element of the Barnetts fleet is the low ground-pressure tires They’ve learned in their own orchards the importance of low ground pressure to avoid ruts that make harvest difficult at best As processor expectations for cleaner fruit grew the Barnetts added a step before loading the bulk trailers This cleaning machine tumbles the crop onto a hedgehog belt before transferring the fruit to a set of Dolman rollers As a final cleaning step jets spray the apples with water before elevating them into the trailers MRB also makes specialty equipment for non-orchard customers services and repairs equipment and fabricates steel-framed buildings Contact: FARM SHOW Followup J H Barnett & Sons Pigeon House Weston Beggard Hereford U K HR1 4BL ph 1432 850431 or Classic Tractor Magazine Sundial House 17 Wickham Rd Beckenham Kent BR3 5JS England www classictractormagazine co uk
To read the rest of this story, download this issue below or click
here to register with your account number.