You have reached your limit of 3 free stories. A story preview is shown instead.
To view more stories
To view more stories
SUBSCRIBE OR RENEW NOW
(If your subscription is current, click here to Login or Register.)2025 - Volume #49, Issue #1, Page #17
[ Sample Stories From This Issue | List of All Stories In This Issue]
Shop-Built Trailer Still Rolling After 25 Years
After building and selling six trailers, Norman Sieting built one that satisfied him. While he eventually sold it to a neighbor, he kept a close eye on it and used it as needed. Recently, he even helped with an upgrade. After 25 years and three deck replacements and repainting, Sieting reports the trailer is still goin..........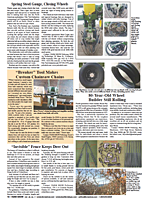
You must sign in, subscribe or renew to see the page.
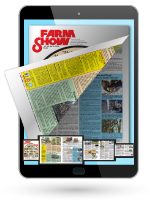
You must sign in, subscribe or renew to see the flip-book
Shop-Built Trailer Still Rolling After 25 Years MISCELLANEOUS EQUIPMENT Miscellaneous After building and selling six trailers Norman Sieting built one that satisfied him While he eventually sold it to a neighbor he kept a close eye on it and used it as needed Recently he even helped with an upgrade After 25 years and three deck replacements and repainting Sieting reports the trailer is still going strong It has traveled as far as Colorado and Tennessee without a problem “I built my first one and a friend begged me to let him buy it ” says Sieting “I built a new one and when I started using it I started building another When I put a deck on the new one the old one would go up for sale Every trailer I built got better ” By the time he built his last trailer an 8 by 16-footer he had an innovative design He started with a 40-ft length of 4 by 6-in 3/8-in angle iron After marking off 16 ft at either end he notched the corners and then started heating them “Once it was hot enough I could bend it by hand with a helper holding the other end of the angle iron ” recalls Sieting “Once I heated and bent the second 16-ft length I had a U-shape frame with 16-ft sides and an 8-ft center ” At the time many trailer house tongues were available at scrap metal prices Sieting bought some and used one as a trailer tongue He cut others into 8-ft lengths each 10 in wide Sieting split them in half lengthwise and welded them in place as 5-in wide frame cross members “I mounted the frame on 7 000-lb tandem axles also salvaged from a house trailer ” says Sieting “I cut out the original mobile home brakes and put in replaceable brakes ” At the rear end he mounted an 8-ft bumper made of Schedule 80 4-in dia pipe Sieting left 4 in between it and the end of the deck so he could wrap chains around it to secure loads The pipe also served as a mounting point for ramps “I cut a short length of the next larger size pipe in half lengthwise and welded each piece to the end of a car ramp ” says Sieting “I could set the ramps in place and slide them to the right position for loading a vehicle ” Sieting wanted a tilting bed To make it he set the trailer house tongue under the first third of the trailer bed and pinned it to the frame This required exact measuring as he first welded two 1-in thick 5 by 8-in steel plates with 1-in dia holes to each side of the frame It also required heating and bending the ends of the V-shaped tongue so they would fit between the plates He notched the 10-in wide tongue members at their midpoint to seat the bed in transit “When a lot of weight is placed on the front end of the trailer it wedges the trailer bed into the notch ” says Sieting Before pinning the tongue to the frame he drilled holes to match those in the steel plates He also welded 4-in boss ring to reinforce each 1-in hole in the tongue “When we mounted the trailer frame to the tongue the steel plates had to fit over the tongue and the bosses and all the holes had to line up exactly ” says Sieting “It was tricky as I was using 1-in bolts so there was no play ” He fabricated hold-downs with stainless steel rods that ride inside pipe welded to the tongue Slots in the pipe allow levers welded to the rods to slide the rods back and rotate them locking them down on tabs welded to the trailer frame Channel iron is welded to the top center of the trailer frame A 2 000-lb marine winch comes on an adapter with slotted holes Studs screwed into holes threaded into the channel iron provide a solid anchor for the winch Sieting welded flat stock with gussets and fenders to the top edges of the 4 by 6-in trailer frame sides This provided a surface for mounting side rails of 2 by 2-in steel tubing “I also built a toolbox into the tongue ” says Sieting “It holds the winch binders and chains ” Although the seventh trailer may have been his best that didn’t mean it couldn’t be improved Recently his neighbor brought it back to Sieting to make a change “We added 20 in to the rear end but sloped it about 5 degrees ” he explains “Now he releases the retainers on the bed and when he drives his front wheels onto the extensions the trailer tilts and he can drive on the rest of the way When he gets past the halfway point it returns to level ” One more change was made to the trailer with its latest upgrade “I always used 2-in thick home-sawn ash for the deck ” says Sieting “This time my neighbor went with manufactured decking The laminated sheets look good and should last a long time ” Contact: FARM SHOW Followup Norman Sieting 6112 Walker Rd NW Rapid City Mich 49676 ph 231-564-1031; normansieting@gmail com
To read the rest of this story, download this issue below or click here to register with your account number.