You have reached your limit of 3 free stories. A story preview is shown instead.
To view more stories
(If your subscription is current,
click here to Login or Register.)
Shop-Built Lathe Better Than New
When the wood lathe he bought chattered with vibration, Norman Sieting got busy and built his own. With 2 by 2-in., 1/4-in. thick angle iron legs and a 4 by 6-in. angle iron bed, he didn’t worry about chatter. He used 1/4-in. H-beam steel for the headstock and tailstock. The lathe is 4 ft. long and can turn a 16-in. pi
..........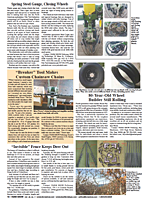
You must sign in, subscribe or renew to see the page.
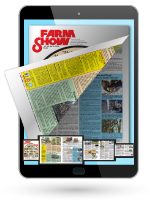
You must sign in, subscribe or renew to see the flip-book
Shop-Built Lathe Better Than New FARM SHOP Tools When the wood lathe he bought chattered with vibration Norman Sieting got busy and built his own With 2 by 2-in 1/4-in thick angle iron legs and a 4 by 6-in angle iron bed he didn’t worry about chatter He used 1/4-in H-beam steel for the headstock and tailstock The lathe is 4 ft long and can turn a 16-in piece of wood All he purchased for the job were the V-belt pulleys bearings and the live center on the tailstock “I used 4-in wide H-beam for the headstock and 3-in wide H-beam for the tailstock and welded base plates to them to bolt to the bed ” says Sieting “I milled a channel out of the tailstock H-beam and mounted the live center on the end of a 1-in threaded rod ” Making the headstock required making room in the center of the H-beam for the pulleys and boring holes in the sides for its spindle Three-in square blocks of 1/2-in steel were welded to either side of the headstock after being bored out for the bearings Sieting milled a brass sprue for the headstock The sprue can be unscrewed and replaced with a 6-in chuck He also made the tool rest It’s a 6-in length of left-over grader blade tapered at each end He mounted it to a shaft on a slotted length of steel that bolts to the bed It’s easily adjusted up or down and in or out The electric motor is mounted on a plate with a short pipe welded to one edge of the underside The pipe rides free on a steel arm welded to the end of the lathe The arm is 1/2-in round stock bent at a right angle around the corner of the lathe When a V-belt is in place the motor’s weight tensions the belt Sieting simply tilts the motor forward to release tension when changing belts With only occasional need for the full 4-ft bed for turning wood Sieting fabricated a 2-ft metal brake to fit on one end of the lathe bed The brake bed is a 24-in long piece of 4 by 6-in angle iron that bolts to the lathe bed The top steel plate is 24 in long 1 by 6 in and tapered at the long edges A 24-in long 1 by 2-in piece of steel is bolted to the top plate from its underside It’s a reinforcing bridge for the top plate tapered at each end “The bridge keeps the top plate flat when pressure is applied to the brake ” says Sieting Turn knobs in the keepers on the ends of the top plate screw into the angle iron bed to hold down the top plate and the material being shaped When the turn knob is loosened springs on bolts that extend through the keepers to the angle iron bed raise the top plate so material can be slid into place The brake apron is a 24-in length of 2 by 3-in bar stock anchored to the keepers at pivot points A lever on the apron provides the leverage needed to bend most metal Sieting works with Contact: FARM SHOW Followup Norman Sieting 6112 Walker Rd NW Rapid City Mich 49676 ph 231-564-1031; normansieting@gmail com
To read the rest of this story, download this issue below or click
here to register with your account number.