You have reached your limit of 3 free stories. A story preview is shown instead.
To view more stories
(If your subscription is current,
click here to Login or Register.)
Self-Guiding System For 3-Pt Cultivators
Latest new self-guiding system for precision, high speed cultivation of row crops is a "tilted wheel" concept introduced by Bezzerides Brothers, Orosi, Cal.
"Most farmers who grow row crops - whether corn, soybeans, cotton or vegetable crops - can easily adapt this system to their existing 3-pt. cultivator, allo
..........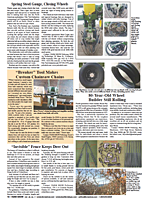
You must sign in, subscribe or renew to see the page.
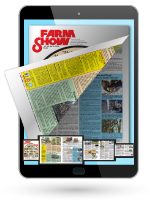
You must sign in, subscribe or renew to see the flip-book
Self-Guiding System For 3-Pt Cultivators CULTIVATORS Cultivators (58C) 7-3-36 Latest new self-guiding system for precision, high speed cultivation of row crops is a "tilted wheel" concept introduced by Bezzerides Brothers, Orosi, Cal.
"Most farmers who grow row crops ù whether corn, soybeans, cotton or vegetable crops ù can easily adapt this system to their existing 3-pt. cultivator, allowing them to travel at speeds up to 8 or 9 mph, even on the first cultivation when plants are small," explains Paul Bezzerides, inventor. "The system readily adapts to all types of row-crop planting ù whether on beds, furrows, ridges or level ground."
Here's how the patented mechanical guidance system works:
The basic unit consists of a "tilted" rubber tired gauge wheel and a companion furrowing shoe. The wheel, 8 in. in dia. and mounted on the spindle at a 33? angle, travels in the freshly-made groove made by the shoe mounted directly ahead of it. Except for extremely wide cultivators, one pair of tilted guide wheels ù one mounted on the left side of the machine and the other on the right side ù guides the cultivator with precision accuracy at high speeds.
"When you come to the field with your 3-pt. cultivator, you remove the blocks to give the cultivator freedom to swing freely on the 3-pt. You then adjust the guide wheels and cornpanion furrowing shoes so the cultivator moves straight down the rows as it's pulled forward," explains Bezzerides. "If it tends to veer to the left, for example, you move the gauge wheels to the right to pull it back so it travels dead-center down the rows. Once adjusted, the tilted guide wheels on the side of the cultivator, traveling in grooves made by the companion furrowers mounted just ahead of them, hold the cultivator in alignment independent of the tractor's exact travel path ù within the "swinging room" distance of the 3-pt. hitch.
"The rows don't have to be planted - absolutely straight ù just so there are no sharp, sudden curves," Bezzerides points out. "The system will also guide the cultivator on hillsides. If the slope is too severe, we suggest mounting a æstinger' support on each side of the cultivator. It's simply a flat plate (8 in. by 24 in. by 1/2 in. thick) welded to a 1 by 3 in. standard to stabilize the end of the cultivator. If the hillside slope is to the left, for example, you would drive slightly to the right, says Bezzerides.
"The guidance system is easier to understand if you think of the furrowers and guide wheels working together to lay down a pair of railroad tracks parallel to the crop rows. The cultivator, riding on these rails, is self-guiding, steering itself with precision accuracy at much faster than normal speeds ù even in newly emerged crops planted in narrow rows," explains Bezzerides.
A key advantage of the system is that it makes its own fresh groove as it goes down the row and doesn't require any type of existing groove. Another advantage, says Bezzerides, is that the tilted guide wheels turn on roller bearings and thus add very little drag to the tractor's pulling load.
"The guidance system leaves the field furrowed out. If you want level ground between the rows, tools can be added on the rear to smooth out the furrows," Bezzerides points out.
A pair of tilted guide wheels, each complete with rubber tires (4:00 by 8 in.), shank and furrower with bracket that permits the complete unit to be mounted on one tool bar, sells for $385 a pair, right and left. Mounting brackets for wheel and furrower shanks fit standard 2 1/4 in. cultivator frames.
"We've tested the guidance system on several thousand row crop acres during the past two years. We know it works," Bezzerides told FARM SHOW. He holds 17 other patents, most of them on specialized tools for weeding and thinning row crops.
For more information, contact: FARM SHOW Followup, Bezzerides Brothers Inc., P.O. Box 211, Avenue 416 14142, Orosi, Cal. 93647 (ph 209 528-3011).
To read the rest of this story, download this issue below or click
here to register with your account number.