You have reached your limit of 3 free stories. A story preview is shown instead.
To view more stories
(If your subscription is current,
click here to Login or Register.)
Hydraulic-Drive Head Beefs Up SP Mower
"There's nothing like it on the market. It can handle even the thickest hay while traveling at 8 mph with no problems," says Tom Cathey, Covington, Texas, about the "hydraulic-drive" 14-ft. cutterhead he made by completely rebuilding a New Idea 5409 rotary cutterhead and mounting it on his Hesston self-propelled swathe
..........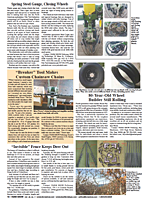
You must sign in, subscribe or renew to see the page.
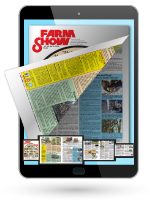
You must sign in, subscribe or renew to see the flip-book
Hydraulic-Drive Head Beefs Up SP Mower HAY & FORAGE HARVESTING Mowers (38) 20-5-3 "There's nothing like it on the market. It can handle even the thickest hay while traveling at 8 mph with no problems," says Tom Cathey, Covington, Texas, about the "hydraulic-drive" 14-ft. cutterhead he made by completely rebuilding a New Idea 5409 rotary cutterhead and mounting it on his Hesston self-propelled swather.
Cathey used a pair of automotive rear ends and a couple of driveshafts to vertically drive the cutterhead. The driveshafts run directly to U-joints welded to the top of the cutting discs. Each shaft powers a set of five discs which rotate at about 3,300 rpm's.
Cathey used the mower this summer for the first time on 200 acres. "It's almost unbelievable how well it cuts. It cost less than $10,000 to build and works beter than commercial mowers that sell for $60,000 or more. One time I used it in thick, knee-high hay and cut 38 acres in less than four hours.
"The mowers lay the hay out in an even layer so it dries quickly. I can often cut hay one day and bale it the next day. The original Hesston cutterhead crimped hay and put it in a windrow that dried unevenly so we lost protein and made lower quality bales."
Cathey felt the New Idea 9-ft. header wasn't built strong enough to handle the increased load so he stripped it down to the discs and used 6-in. sq. steel tubing and 4-in. channel iron to build a new frame for it, extending the cutterbar out to 14 ft. He bought three more used New Idea discs.
He mounted two automotive rear ends on top of the frame, each with one side of the axle removed. He joined the two rear ends together at the center which keeps the two sets of discs running in time with each other. He placed the rear ends so that they both run in reverse and welded the spider gears rigid inside each rear end. Then he installed a driveshaft and roller bearing in-side each outer rear end so he could direct-couple a hydraulic motor to each.
The next step was to run driveshafts from the rear ends down to the cutting discs. "The car driveshafts are equipped with splined slip shafts so that the cutterhead can bounce up and down without damaging the rear ends," notes Cathey.
To power the two hydraulic motors he mounted a pair of hydraulic pumps on back of the tractor that are shaft-driven off the engine flywheel. The mower's original Perkins 75 hp diesel engine didn't have enough power to handle the larger cutterhead so he replaced it with a new Deere 96 hp industrial, turbocharged diesel engine. "The Deere industrial engine uses only about 1 gal. of fuel per acre depending on how heavy the grass is," says Cathey, adding that he put a 1.47 gearbox on the hydraulic pumps to get the ratio needed to drive the cutting discs at 3,300 rpm's.
Steel hydraulic lines run from the pumps on back of the mower up to the motors on the cutterhead and are used to dissipate heat generated by the pump.
Contact: FARM SHOW Followup, Tom Cathey, Box 95, Covington, Texas 76636 (ph 817 854-2333).
To read the rest of this story, download this issue below or click
here to register with your account number.