You have reached your limit of 3 free stories. A story preview is shown instead.
To view more stories
(If your subscription is current,
click here to Login or Register.)
Farmer-Built Drier Works Good As New
Cash cropper Walter Glynn spent a lot of time shopping for a small-scale corn drier two years ago, but even the most persuasive salesman failed to close a deal with this resourceful farmer.
He ended up building his own. His tab for a continuous flow grain drier that can take 100 bu. of 30% corn down to 15% in an
..........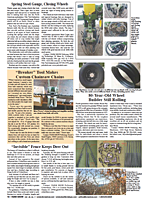
You must sign in, subscribe or renew to see the page.
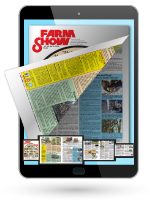
You must sign in, subscribe or renew to see the flip-book
Farmer-Built Drier Works Good As New GRAIN DRYERS Grain Dryers (29E) 8-4-14 Cash cropper Walter Glynn spent a lot of time shopping for a small-scale corn drier two years ago, but even the most persuasive salesman failed to close a deal with this resourceful farmer.
He ended up building his own. His tab for a continuous flow grain drier that can take 100 bu. of 30% corn down to 15% in an hour ran to $4,000. All parts were new except for the blower fan, which he pulled off an old grain bin. A comparable factory-made model, he estimates, would have cost somewhere in the neighborhood of $15,000.
For years, the Haldimand County, Ont., farmer made do with a pto driven drier. Drying was uneven and expensive, so Glynn decided to build his own machine to dry his 75 acres of corn.
The sheet metal outer walls of his homemade drier are 17 ft. high, with an extra 10 in. of 1/4-in. plywood sheet that clips onto the metal at the top. Glynn bought 10 ft. lengths of perforated tobacco kiln floor to form 2 drying columns 10 ft. high, 8 ft. long and one foot wide. The drier holds 160 bu. at a time. Glynn fills it to the top of the inverted v-shaped baffle over the drying column so that hot air doesn't escape.
The drier has 2 heat sensors. One, near the top of the drying column, is set for 180?F and another, 3 ft. from the bottom, is set at 130?F for 30% corn. The lower sensor regulates the action of metering rolls that dump the grain into an auger leading to the storage bin.
Borrowing designs he had noted on new equipment, Glynn opted for homemade metering rolls (rather than a pair of augers running along the length of the drying columns) so that the grain would empty evenly. He used 1 in. pipe for the rolls and welded 4 ft. long "kickers" along the length of the pipe. The rolls are powered by a 1/4 hp electric motor through a 50:1 reduction gear.
To minimize propane costs, Glynn also installed 3 lengths of 6 in. dia. flexible pipe to draw hot air from the bottom of the columns to the back of the burner. The heat exchanger pays off most days, especially when the 80?F waste heat warms outside air from 50?F in October. When the weather is particularly humid, the exchanger is of limited value. "But you don't get much efficiency out of your propane anyway, when there's too much moisture in the air," notes Glynn.
He's used the drier for only one season, and when he first filled the rig, he noticed that the walls soon started to bulge a little from the weight of the grain. He quickly welded some angle iron along the sides for extra support.
"I can hardly believe it turned out so well," says Glynn, although if he had to do it over again, he probably would have added a pressure switch on the top of the loading auger to prevent spillage while he's out harvesting the next load with his 12-year-old, 10 ft. IH combine. Glynn also plans to put a concrete pad under the drier.
Last year, he dried all his corn to 15.0 to 15.5% moisture by taking it down to 17% in the drier and using an aeration bin for the final stage of dry down. And the cost? Glynn now dries his 30% grain corn to 15% for 17 cents a bushel, less than half the usual elevator drying fees.
Reprinted with permission from Country Guide Magazine, Winnipeg, Canada.
To read the rest of this story, download this issue below or click
here to register with your account number.