1991 - Volume #15, Issue #5, Page #18
[ Sample Stories From This Issue | List of All Stories In This Issue | Print this story
| Read this issue]
Mini-Thresher
![]() |
Rahn built the 29-in. long by 10-in. high thresher from 22-ga. galvanized steel, brass, and aluminum which he used for the pulleys and belt tighteners. Vinyl seat covering was used for the belts. His "mini thresher" took first place honors at county and state fairs last year.
"I had wanted to build a mini thresher for many years," says Rahn, who grew up on a farm. "One day on a trip to Arizona I happened to see a Minneapolis Moline Special sitting alongside a Kansas road. I took several photos of it, then on the way back from Arizona I took more close-up photos. It took 400 hours to build. I used a mill and lathe and made my own sheet metal brake to bend the metal. The feed conveyor is hinged just like on the real thresher so it can be folded up for transport. A set of cam-operated brass twine cutters are mounted on top of the conveyor. The cam shaft arrangement was the most difficult part to build."
The thresher's 12-in. long blower can be swung from side to side and raised and lowered by a pair of thumb screws at the rear of the machine. There's a brass ladder on back that was designed to let the operator climb on top of the thresher. The telescoping hitch is built just like the real one and can be extended by pulling a pin. "Extending the hitch allowed the operator to move the thresher in the field without having to fold up the feed conveyor," says Rahn, who used brass chain and slats to make the feed conveyor chain. There's even a straw rack in-side the machine.
According to Rahn, the first Minneapolis Moline Specials were built with an unloading auger that dropped grain through a pair of tubes into sacks. "I remember as a kid watching my dad and another operator take turns filling sacks. Later the company switched to truck-loading augers like the one on my model. The grain elevator unloaded into a dump bucket. As soon as grain filled the bucket, It dumped its load into the unloading auger. It kept track of the number of dumps so that at the end of the day you could figure how many bushels had been threshed."
Rahn made the thresher's wheels by cutting off the ends of 2-in. dia. steel pipe. He used brass rod to make the wheel spokes and axles.
Contact: FARM SHOW Followup, Ray Rahn, 3855 145th St. E., Rosemount, Minn. 55068 (ph 612 437-7935).
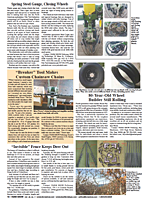
Click here to download page story appeared in.
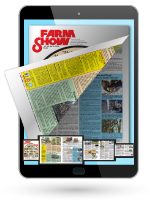
Click here to read entire issue
To read the rest of this story, download this issue below or click here to register with your account number.