You have reached your limit of 3 free stories. A story preview is shown instead.
To view more stories
(If your subscription is current,
click here to Login or Register.)
Double Drive Swather Sicklebar
Leonard Possberg, Humboldt, Sask., converted a conventional swather into a "super swather" by splitting the machine's 34-ft. long sicklebar in two and fitting the "extra" sickle with its own hydraulic motor.
Possberg bought his Massey-Ferguson 200 self-propelled swather equipped with the 34-ft. header four years
..........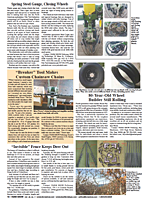
You must sign in, subscribe or renew to see the page.
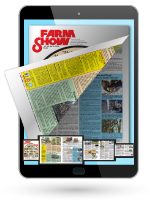
You must sign in, subscribe or renew to see the flip-book
Double Drive Swather Sicklebar HAY & FORAGE HARVESTING Mowers (38) 19-4-40 Leonard Possberg, Humboldt, Sask., converted a conventional swather into a "super swather" by splitting the machine's 34-ft. long sicklebar in two and fitting the "extra" sickle with its own hydraulic motor.
Possberg bought his Massey-Ferguson 200 self-propelled swather equipped with the 34-ft. header four years ago. "I came up with the idea of cutting the sicklebar in two because the original sicklebar broke a lot. It took a lot of time and money to re-pair and I was limited to swathing only in drier conditions."
He cut the sicklebar so that one section is 14 ft. long and the other 20 ft. He mounted a hydraulic motor on the right side of the header along with an extra hydraulic oil reservoir.
The knives run completely independently of each other. To keep them from hitting he added an extra 3-sickle section to the 14-ft. section, turning the three sickle sections upside down so they would run smoothly against the underside of the out-side three sections on the other sicklebar. He used flat head bolts on the inverted sickle sections and widened out the sickle guards to make room for the doubled-up sections.
"I used it for the first time last year and was very pleased with it," says Possberg. "I was able to cut in almost any moisture condition and to cut everything from ripe grain to tough slough grass. I was concerned that the two sicklebars running together could cause a lot of vibration, but I don't feel much extra vibration at all."
Contact: FARM SHOW Followup, Leonard Possberg, Box 1658, Humboldt, Sask., Canada SOK 2A0 (ph 306 682-3744).
To read the rest of this story, download this issue below or click
here to register with your account number.