You have reached your limit of 3 free stories. A story preview is shown instead.
To view more stories
(If your subscription is current,
click here to Login or Register.)
Roto-Tiller Built From Old Combine Cylinder
Saskatchewan farmer Mike Hango, wanted a rototiller for his garden and to work the ground up around rows of trees. He didn't want to spend the money for a commercial one so he built his own 3-pt., 6-ft. wide model using the threshing cylinder and other parts out of a junked-out Deere 65 pull-type combine.
He rem
..........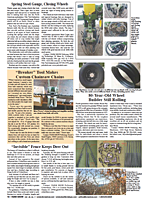
You must sign in, subscribe or renew to see the page.
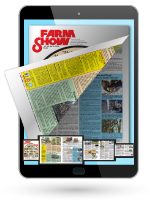
You must sign in, subscribe or renew to see the flip-book
Roto-Tiller Built From Old Combine Cylinder COMBINES Conversions 19-3-2 Saskatchewan farmer Mike Hango, wanted a rototiller for his garden and to work the ground up around rows of trees. He didn't want to spend the money for a commercial one so he built his own 3-pt., 6-ft. wide model using the threshing cylinder and other parts out of a junked-out Deere 65 pull-type combine.
He removed the 40-in. long threshing cylinder and stripped it down to the shaft, keeping the bearings and part of the steel frame on each end of the cylinder shaft. He cut the shaft in half and welded each end into a 3 1/2-in. dia., 5-ft. long, 1/2-in. wall steel pipe. He cut round discs out of 1/4-in. steel plate and welded pairs of them together, then had a machine shop punch holes in them. He then welded the discs onto the pipe and bolted commercial roto-tiller blades onto them.
He used 1/4-in. thick scrap sheet metal to make the hood and bolted the combine's pto-driven gearbox on top of it. The gear-box drives a shaft that double chain-drives a pair of sprockets (the sprockets and chains originally were used to drive the combine cylinder).
"It does a good job of working manure into my garden and comes in handy for digging up prairie grass where I want to plant trees. I spent only about $500 to build it,"
says Hango, who pulls the roto-tiller behind his 35 hp Deere 1040 tractor. "I bought all of the combine parts at a sale for $20. The rest of the money was for new roto-tiller blades. A hinged "door" on the back side keeps dirt from flying out the back side of the machine and helps to level the ground. The rig is offset to one side so I can work the ground close to trees without having tree branches in the way. Each blade is mounted slightly ahead of the one next to it, forming a slight spiral pattern that keeps all the blades from hitting the ground at the same time so they don't bounce up and down too much.
"I had been using an old field cultivator that I cut down to a 7 ft. width. However, it didn't do as nice a job of tilling the garden and in hard ground the tines tended to come up out of the ground. Also, it didn't do a good job of breaking up grass that crept into the edges of my garden.
"The only problem is that the blades can go only about 3 in. deep. If I want to till 6 in. deep I have to make two passes. The problem is that the bottom of the chain guard drags on the ground and prevents the blades from going deeper. Next time I'd use a smaller drive sprocket at the bottom."
The cylinder shaft was smaller in diameter than the hole inside the pipe so Hango had collars machined out to fit inside the pipe before he welded the shaft in. He made the chain guard by cutting out a cardboard template and transferring it to sheet metal. He had a machine shop bend 5/8-in. thick sheet metal to make the 3-pt. hitch. A l 1/ 2-in. long, 3-in. wide steel skid on one side of the rig can be adjusted up or down by repositioning bolts in the skid legs.
Contact: FARM SHOW Followup, Mike Hango, Box 56, Handel, Sask., Canada SOK 1 YO (ph 306 658-4222).
To read the rest of this story, download this issue below or click
here to register with your account number.