You have reached your limit of 3 free stories. A story preview is shown instead.
To view more stories
(If your subscription is current,
click here to Login or Register.)
On The Go Adjuster For Combine Stripper Plates
"It took me 5 years to figure it out. Now I wouldn't combine without it," says Ontario farmer Norman Caron who's engineered a first-of-its-kind hydraulically-operated stripper plate adjusting system that lets him adjust spacing "on the go" between the two stripper plates above the snapper rollers on each row of his cor
..........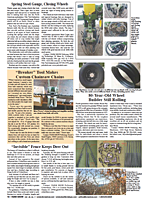
You must sign in, subscribe or renew to see the page.
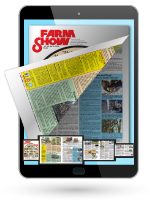
You must sign in, subscribe or renew to see the flip-book
On the go adjuster for combine stripper plates COMBINES Accessories 15-1-16 "It took me 5 years to figure it out. Now I wouldn't combine without it," says Ontario farmer Norman Caron who's engineered a first-of-its-kind hydraulically-operated stripper plate adjusting system that lets him adjust spacing "on the go" between the two stripper plates above the snapper rollers on each row of his cornhead. A single lever in the cab adjusts all rows on his head at once.
"There's never been a quick way to change the size of the opening above the snapper rollers as conditions change in the field or when you move from one variety to another. Now we can open or close the stripper plates on the go if, for example, stalks are smaller on one end fo a field than the other or if it's wet in the morning or dry in the afternoon. When set correctly the stripper plates should hit the butt end of the cob. If they're set too nan: ow you can break off stalks and if they're set too wide you can damage kernels. Now I fmd myself making constant adjustments on the go. Once you start using it it's easy to see when you've got it set right," says Caron, who custom-harvests seed corn in addition to running his own large operation. "I was tired of manually changing all the plates between jobs and couldn't afford the time it took."
Caron mounted a graduated scale on top of the head that he can easily see from the cab. The scale is marked in 1/16-in. increments. When the indicator is at the center line, the plates are set 1 in. apart.
"We didn't have any problems during 1,000 acres of harvesting last fall. It's a very simple design with minimal linkage so it requires little maintenance. It was a real time and crop saver that easily paid for itself," says Caron, noting that one unexpected use he found for the adjuster was as an "unplugger". If crop material starts plugging up he just opens the plates up wide and lets everything go down through.
The adjuster system is mounted on Caron's New Idea Uni System 844 cornhead but could be installed on any size or make of head.
"The only commercially-produced cornhead on the market with hydraulically-adjusted stripper plates is the Geringhoff head from Germany. The problem with that system is that it only adjusts one plate, so the gap is not centered above the snapping rollers. We adjust both stripper plates," says Caron.
An adjusting mechanism mounts directly under each snout, exactly between every two rows. It consists of a rotating shaft with two linkage arms attached to each end of it that in turn attach to the stripper plates on each side. A bracket runs from each rotating shaft to a length of 2-in. sq. tubing beneath the snouts that runs across the full width of the header. A single 8-in. stroke hydraulic cylinder slides the tubing back and forth, turning the rotating shafts which open or close the stripper plates.
The end of each linkage rod is threaded to allow precise manual adjustment of all the plates so they can be set with the same gap front and back. "I prefer to set the back slightly wider than the front to prevent wedging of material. Once set, they all open and close simultaneously at exactly the same width," says Caron, noting that he's applied for U.S. and Canadian patents and hopes to sell the idea to a major manufacturer. The system can also be easily adapted to existing cornheads and he would like to hear by mail from readers interested in having a system installed on their cornhead.
For more information, contact: FARM SHOW Followup, Norm Caron, Rt. 1, Grande Point, Ontario, Canada NOP ISO.
To read the rest of this story, download this issue below or click
here to register with your account number.