1980 - Volume #4, Issue #5, Page #35
[ Sample Stories From This Issue | List of All Stories In This Issue | Print this story
| Read this issue]
Make A Rope Wick Applicator
![]() |
Several manufacturers make rope wick applicators, and many farmers have assembled their own units. Mike Culp, Dorchester County Extension Agent headquartered at St.eoTge, S.C.; helped brothers, Doug and J.C. Reeves make a simple, straight line applicator that mounts on a tractor 3-pt. hitch. Neighbors liked it so well that they've kept the Reeves brothers busy with orders for similar custom-built units.
In Lyons County, Iowa, Howard Mogler and his son Brian built a zigzag type and mounted it on the front of their tractor for easier viewing.
Culp-Reeves Applicator
Culp and the Reeves brothers used straight 3-in. PVC pipe (13 ft. for a 4-row unit; 19 ft. for 6 rows) and marked two chalk lines 11/2 in. apart the length of the pipe. Holes (49/64 in. dia.) forinserting the rope were drilled along each chalk line. Individual rope sections are 12 in. long with a 3 in. spacing between sections. A key design feature is that the rope sections overlap in the two rows so there are no skips for weeds to slip through without exposure to the chemical.
The Reeves brothers screwed
1/2 x 1/2 in. brass compression fittings into each hole and made sure the fittings were straight before tightening. Half-inch soft braided nylon rope was cut into 20 in. lengths (20 pieces for a 13-ft. wide applicator) and the ends seared with a butane torch to prevent unraveling. Two 1/2 in. brass compression nuts were slipped onto each rope and a 1/2 in. rubber 0-ring washer was placed 3 in. from each end. Rope
ends were inserted into the applicator compression fittings and the nuts tightened over the 0-rings. (Avoid overtightening).
A 3-in. PVC pipe plug was cemented to one end of the pipe and a 3-in. PVC elbow with removable plug (to fill and drain the applicator) was attached to the other end. The applicator was clamped to a 3-point hitch A-frame and tool bar and filled with spray solution (1 gal. Roundup per 2 gal. water). Travel speed is 2 to 4 mph, depending on severity of the weed problem.
Mogler Applicator
Some users complain that "straight" wick applicators tend to whip tall weeds, and on sloping terrain permit chemical to run to one end where it drips while the other end dries up.
Howard and Brian Mogler designed their applicator to avoid both problems. Instead of using straight pipe, they built a "V-shape" for each row, then plugged the pipe between row units. Howard says the V-shape provides about one-third more total applicator length compared to a straight pipe.
The Moglers used 21/2-in. PVC pipe with 90? elbows at each point of the "V's". To provide separate compartments for each row, they carefully cut circles from the bottoms or lids of sturdy plastic buckets and pushed them against a shoulder inside the elbows located at the forward points of the "V's" (between crop rows). The back side of these disks was sealed with caulking compound, and a 1/z-inj ring of 21/2-in. PVC pipe was cemented in on the other side to keep disks from moving during applicator assembly.
The Moglers used 20-in. pieces of nylon rope, but holes for each rope piece were drilled only 71/4-in. apart. So, more rope is required for their applicator than the Gulp-Reeves model. Rows of holes were placed 1 in, apart on the pipe. Also, instead of using brass compression fittings, the Moglers drilled 3/4-in. holes and installed rubber grommets with 1/z-inj holes. Grommets were sealed with 3M weather-stripping cement which Mogler says appears to be unaffected by the chemical.
He acknowledges that brass compression fittings may provide a better seal and greater durability than the rubber grommets which he and his son used. However, their lower-cost design "worked great" on 1,800 to 2,000 acres of use this past summer.
Removable fill and drain plugs were installed in each row section, but fill plugs were not vented as they are on some applicato
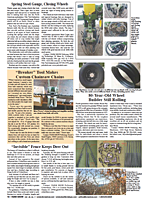
Click here to download page story appeared in.
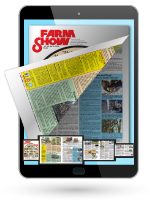
Click here to read entire issue
To read the rest of this story, download this issue below or click here to register with your account number.