Homemade Culvert Windmill
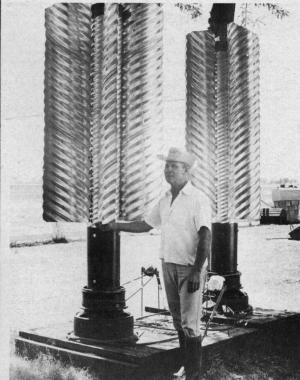 ✖  |
"There's millions of dollars of machinery and parts going to waste in junkyards around the country," says Dick Graf, Emerson, Idaho, whose homemade culvert wind machine, built almost entirely from salvaged parts, generates electricity to help heat his house.
Using old wheels with hubs and bearings, and pieces of steel pipe, Graf took his main ingredient ù 10-in. dia. metal culverts ù and made several wind machines that generate electricity whenever wind blows through his farmstead.
Graf cut 8-ft. lengths of the culvert lengthwise into two equal-sized pieces and bolted these to 8-ft. lengths of steel pipe so that the culvert pieces form half circles to catch the wind. He then welded a car wheel, complete with hub and bearing, onto a truck wheel for support and mounted the steel pipe, with culvert attached, into the hub like a vertical axle.
Standing two of these windmill turbines on end about 10 ft. apart, he joined the two together with a nylon belt so they run together as the wind blows. A V-belt off one of the turbines drives a used 12-V auto generator. Electricity from the generator powers a "heat box" in his basement which contains automotive headlights, also salvaged, that Graf says generate as much heat as a small wood stove.
Besides the two smaller windmills, Graf has also built a larger 18-ft. model which he suspends from the end of an unused hay derrick on his barn. This larger unit is used to power an air compressor which builds up pressures of 100 psi. Graf says one advantage of the design is that the machines can be mounted vertically, or horizontally along the peak of a barn roof or other structure.
Graf says the trick to building the culvert windmill is to cut the culvert exactly down the middle. He uses a $20 carbon steel bit to cut the pieces then weighs them and trims them until they are of equal weight and will balance themselves out on either side of the windmill's center shaft.
Graf says that although each of his windmills now has 4 louvers, he plans to outfit his next one with five. All in all, he has spent less than $300 for parts. He's working on a protective device which will shut down the windmills automatically in extremely high winds to prevent them from being damaged.
For more information, contact: Dick Graf, 850 W. 340 S., Heyburn, Idaho 83336 (ph 208 678-5717).
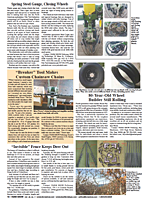
Click here to download page story appeared in.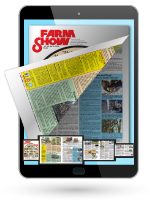
Click here to read entire issue
Homemade Culvert Windmill ENERGY Wind Power 6-6-7 "There's millions of dollars of machinery and parts going to waste in junkyards around the country," says Dick Graf, Emerson, Idaho, whose homemade culvert wind machine, built almost entirely from salvaged parts, generates electricity to help heat his house.
Using old wheels with hubs and bearings, and pieces of steel pipe, Graf took his main ingredient ù 10-in. dia. metal culverts ù and made several wind machines that generate electricity whenever wind blows through his farmstead.
Graf cut 8-ft. lengths of the culvert lengthwise into two equal-sized pieces and bolted these to 8-ft. lengths of steel pipe so that the culvert pieces form half circles to catch the wind. He then welded a car wheel, complete with hub and bearing, onto a truck wheel for support and mounted the steel pipe, with culvert attached, into the hub like a vertical axle.
Standing two of these windmill turbines on end about 10 ft. apart, he joined the two together with a nylon belt so they run together as the wind blows. A V-belt off one of the turbines drives a used 12-V auto generator. Electricity from the generator powers a "heat box" in his basement which contains automotive headlights, also salvaged, that Graf says generate as much heat as a small wood stove.
Besides the two smaller windmills, Graf has also built a larger 18-ft. model which he suspends from the end of an unused hay derrick on his barn. This larger unit is used to power an air compressor which builds up pressures of 100 psi. Graf says one advantage of the design is that the machines can be mounted vertically, or horizontally along the peak of a barn roof or other structure.
Graf says the trick to building the culvert windmill is to cut the culvert exactly down the middle. He uses a $20 carbon steel bit to cut the pieces then weighs them and trims them until they are of equal weight and will balance themselves out on either side of the windmill's center shaft.
Graf says that although each of his windmills now has 4 louvers, he plans to outfit his next one with five. All in all, he has spent less than $300 for parts. He's working on a protective device which will shut down the windmills automatically in extremely high winds to prevent them from being damaged.
For more information, contact: Dick Graf, 850 W. 340 S., Heyburn, Idaho 83336 (ph 208 678-5717).
To read the rest of this story, download this issue below or click
here to register with your account number.