1978 - Volume #2, Issue #3, Page #01
[ Sample Stories From This Issue | List of All Stories In This Issue | Print this story
| Read this issue]
New Baling Breakthrough
![]() |
and 151/2 in. high.
The new-style Steffen Systems baler was extensively field tested last fall and will be operating this summer in Oregon's Willamette Valley east of Salem. Stan, who lives near Silverton, extends a personal invitation to any interested FARM SHOW readers to come and see this first-ofits-kind baler in its working clothes.
Dimensions of the baling chamber are 90 in. wide, 16 ft. long and 151/2 in. high. Individual alfalfa bales weigh right at 1,000 lbs. and are tied with 10 wires. "We used conventional knotters and knotting functions and simply ganged units designed for conventional balers to get the necessary width for our extra wide bale," explains Stan.
When a bale is made to a preset density, a limit switch kicks in and the bale is automatically lowered to the ground on the go via a hydraulic ally-operated platform. It makes a 1,000 lb. bale at the rate of about one per minute.
"In good alfalfa, manufacturers of the biggest conventional balers advertise that their machines will do 30 tons per hour. If they'll do 30 tons, this one will do at least 45 tons under the same conditions," says Stan. He notes that a bale wagon working in conjunction with two large conventional balers can bale, haul, and stack about 200 tons of alfalfa a day. "We can handle as much hay, using only one baler and two men - one to run the baler and one to load the bales with a front end tractor loader. The man handling the bales behind the baler loads them on and off flatbeds with a conventional tractor-mounted front end loader equipped with a special fork," Stan explains.
The bales can be stacked alone, or in combination with conventional bales. They can be stacked any place a tractor loader can get to. For feeding; the bales are handled with a fork which has 20 curved teeth that bite about 6 in. into the bale. The bales remain intact when the wires are removed. Even without wires, they can be lifted into a tub grinder for processing, dropped into a feeder, or dropped and scattered on the ground for feeding.
"We plan to build a special wagon for mechanical feeding of the big flat bales," Stan told FARM SHOW. He notes that the prototype baler was used on about 500 tons of straw last fall, and a lesser amount of alfalfa.
Here, according to Stan, are other design features of his new-style baler:
Hay is gathered from two or three windrows by rake wheels on each side of the baler pickup. The wheels will also feed mowed but unraked material into the baler. The pickup drum, powered by a Char-Lynn orbit motor at 80 rpm, is 7 ft. wide and uses rubber mounted teeth spaced 3 in. apart. Hay is transferred to a pair of 12 in. dia. feed rolls which spread the material before it's moved into the chamber by the feed arm. The feed arm is operated by a pair of 2 in. dia. cylinders which are rubber cushioned for shock absorption. The bottom of the plunger has 5/s in. thick knives to cut incoming hay off with each plunger stroke. The plunger face has ten slots for needles to pass through when tying.
Wire tying is accomplished using ten needles and ten twister shafts driven from a special-built bevel gear case. The wire cutter and gripper are operated by a hydraulic cylinder. Timing is controlled by limit switches operating electric valves in the hydraulic system. Racks on each side of the cab carry 20 boxes of wire.
"Bale extrusion is controlled by upper and lower tension rails made from 4 in. I-beams," explains Stan. "Two 4 in. cylinders pull these beams in against the bale. Pressure is regulated by a relief valve inside the cab. The bale is then delivered onto the carrying chute, which lowers to the ground hydraulically when the bale is completely out of the chamber."
Power for the new-style baler is provided by a Perkins 354 cu. in. turbo-charged diesel, the same one used in the Massey Ferguson 7600 comb
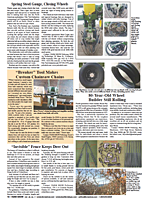
Click here to download page story appeared in.
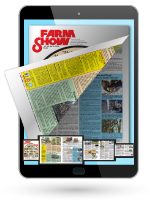
Click here to read entire issue
To read the rest of this story, download this issue below or click here to register with your account number.