You have reached your limit of 3 free stories. A story preview is shown instead.
To view more stories
(If your subscription is current,
click here to Login or Register.)
Tracked Backhoe As Good As Factory-Built
"Ever since tracked backhoes came out I've been fascinated by them and was bound and determined to have one," says Gary Arnold, a machinist from rural Marietta, Ohio. "I started looking at commercial models to see what parts I'd need to build my own. Then I gathered the necessary parts, from junk yards mostly, and buil
..........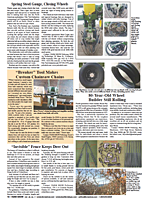
You must sign in, subscribe or renew to see the page.
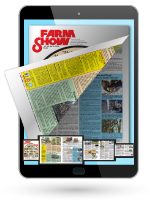
You must sign in, subscribe or renew to see the flip-book
Tracked Backhoe As Good As Factory-Built MISCELLANEOUS EQUIPMENT Earth Movers 19-1-9 "Ever since tracked backhoes came out I've been fascinated by them and was bound and determined to have one," says Gary Arnold, a machinist from rural Marietta, Ohio. "I started looking at commercial models to see what parts I'd need to build my own. Then I gathered the necessary parts, from junk yards mostly, and built it over about two years.
"I've used it to dig footings and septic tank holes. It works just as good as a commercial rig," Arnold says. "I don't think I've got more than $2,000 in it. A factory-built machine would have cost me at least $15,000."
An 18 hp. 2-cyl. Wisconsin engine out of an old trenching machine powers Arnold's backhoe, which is 48 in. wide and weighs 5,000 lbs.
Tracks on the vehicle are 60 in. long by 10 in. wide. Arnold made them from drive chains off a rock drill, used in coal mining, that someone gave him. Pads are made from bar steel with square stock welded on for cleats. Track frames were also made from bar steel and rollers are fabricated from tubing and plate steel.
"After first building the tracks and track frames, I built the rest of the machine to correspond with the tracks and undercarriage," Arnold says.
The center pin the machine turns on was built using a rear end and wheel hub from a 44-ton truck. The spindle is welded into the lower track frame and the cab frame bolts to the wheel hub. The machine pivots a full 360 degrees. The boom is made from 3/16-in. and 1/4-in. plate steel with gussets as needed. It has a digging depth of 100 in. and a reach of 144 in.
"The hardest part of building the back-hoe was figuring out the boom - center points, proper travel, the correct pump, valve and cylinder capacity to push the bucket into the ground - of the boom," says Arnold. "I'm not an engineer, so I did it the old farm boy way. I made a model out of wood and tweaked it until it worked the way I wanted."
Arnold's design for the machine's hydraulic system, made from off-the-shelf parts, is about the only thing that differentiates it from a commercial backhoe. Arnold installed a single hydraulic pump with flow divider on the machine's motor. "That gives it two live oil circuits so I can do all the same operations a commercial unit does," notes Arnold.
Arnold chose the single pump because it doesn't require as much power as a double hydraulic pump. Arnold was concerned that his machine wouldn't have enough power if he used the double pump arrangement, but says if he were to build another back-hoe he'd use the latter design since commercial backhoes don't have much bigger engines than his.
Contact: FARM SHOW Followup, Gary Arnold, R.R. 2, Box 410, Marietta, Ohio 45750 (ph 614-373-5313 or 896-3010).
To read the rest of this story, download this issue below or click
here to register with your account number.