You have reached your limit of 3 free stories. A story preview is shown instead.
To view more stories
(If your subscription is current,
click here to Login or Register.)
Straw Fired Burner Cuts Drying Costs
Illinois farmer Terry Greer, of Arenzville, is pleased with the results he's been getting with the home-made straw-fired burner he uses to dry corn. A pork producer, Greer also anticipates using the burner to heat his farrowing house next winter.
Taking a cue from today's modern wood stoves, Greer made his burner
..........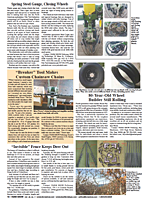
You must sign in, subscribe or renew to see the page.
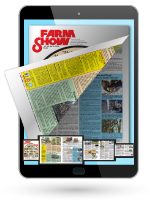
You must sign in, subscribe or renew to see the flip-book
Straw Fired Burner Cuts Drying Costs CROPS Straw 7-5-6 Illinois farmer Terry Greer, of Arenzville, is pleased with the results he's been getting with the home-made straw-fired burner he uses to dry corn. A pork producer, Greer also anticipates using the burner to heat his farrowing house next winter.
Taking a cue from today's modern wood stoves, Greer made his burner air tight and equipped it with a forced air draft and thermostatic controls, enabling him to control air going into his corn at a temperature range of 120 to 130?. A back-up LP burner kicks in if temperature from the burner drops below 120?.
Greer generally uses wheat straw bales to fire the burner but says corn stalk bales, soybean residue, wood or other biomass would work just as well.
"One of the most surprising aspects of the burner's performance is that it burns so clean. I thought I was going to have to regularly clean out ashes. But last fall we dried 38,000 bu. of corn with it and we never cleaned it once," Greer told FARM SHOW. "The fire burns so clean there's hardly any smoke, and absolutely no smoke smell ever gets into the corn."
The large burner is covered with a shroud so that heated air between the burner and the shroud is drawn off the far end, then blown into a drying bin with a full perforated floor.
The burner, made from a salvaged fertilizer tank, is 21 ft. long and 10 ft. in dia.
The big tank has a 2-in. flange and the doors were shaped to fit over it. In between, Greer attached asbestos gasket rope which he bought from a local wood stove dealer. The doors close in the center and are held tightly closed by C-clamps gripped to the flange.
Even though it's virtually air tight, Greer says enough air seeps into the burner to keep the fire from going out entirely.
He notes that last fall, the straw-fired burner enabled him to remove an average of 8 points of moisture from corn for a cost of only 2.86ó per bu. Of that, 0.5ó was for electricity to run a 10-hp fan on the 24-ft. drying bin. "If I'd used LP gas only, the drying cost would have been at least 10ó per bu.," says Greer.
He puts in three big bales at 7 a.m., then another three bales at 7 p.m. He uses a loader to boost them into the burner, three in a row.
"Forced air draft is the real secret to successful operation of the burner," notes Greer. He ran a 4-in. dia. pipe the length of the burner (locating it off to the lower left side) and across the end. Every 24 in. there is a perforation in the pipe, with increasingly larger perforations from front to back.
Outside the tank, also at the lower left, Greer installed a 1 hp squirrel cage fan. It blows air through the perforated pipe and controls the rate of burning. There is a heat sensor and electrical control on the plenum located at the back end of the burner. The control signals to the fan to start at 120? and to stop at 130?. An LP burner kicks in to provide heat until a new batch of bales heats incoming air to 120?.
The entire burner is mounted on a framework of I-beams salvaged from a steel bridge. It's equipped with stub axles on the sides and a stub tongue up front, making it easy to move from job to job.
Greer figures the material used to build the burner cost about $1,500.
To read the rest of this story, download this issue below or click
here to register with your account number.