You have reached your limit of 3 free stories. A story preview is shown instead.
To view more stories
(If your subscription is current,
click here to Login or Register.)
Farmer-Built Cadillac Of Ear Corn Pickers
"My homebuilt ear corn picker outperforms any commercial picker on the market," says Douglas McGill, Reynolds, Ind, who mounted two 12-roll New Idea 737 husking beds on the frame of a Deere 7700 combine.
"Rather than spend about $40,000 for a new Uni-Harvester tractor and $15,000 for anew husking bed, I built my
..........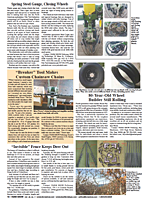
You must sign in, subscribe or renew to see the page.
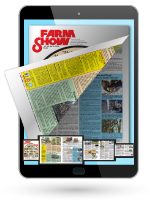
You must sign in, subscribe or renew to see the flip-book
Farmer-Built Cadillac of Ear Corn Pickers COMBINES Corn Pickers 13 My home-built ear corn picker outperforms any commercial picker on the market says Douglas McGill Reynolds Ind who mounted two 12-roll New Idea 737 husking beds on the frame of a Deere 7700 combine Rather than spend about $40 000 for a new Uni-Harvester tractor and $15 000 for anew husking bed I built my own for about $18 000 says McGill who previously operateda 1976 Uni-Harvester 704 equipped with a 1981 Uni-Harvester husking bed I grew impatient with the maintenance and repairs necessary on that unit Also this rig s two husking beds give it twice the capacity of my old machine McGill uses the home-built rig to pick popcorn but says it would work equally well for picking field corn or seed corn You can buy used Deere 7700 combines built in the early 1970 s for less than $10 000 I paid $6 000 for my 1976 model Smaller farmers could equip the combine with only a single 737 husking bed and still gain many of the advantages of this unit McGill also mounted a sheller unit from a Uni-Harvester on his home-built picker I use it to reclaim the small popcorn ears that are lost in the stalk-clearing rollers of the husking beds However you could use it as a stationary sheller by removing the drive belts from the husking beds and disengaging the clutch on the header so that only the sheller would operate A small elevator could deliver corn into the sheller McGill made use of the front half of the Deere 7700 combine equipped with a 6-row 30-in Corn Saver header The two husking beds mount just behind the cab with the sheller mounted between and above them and slightly to the rear McGill says he was disatisfied with his Uni-Harvester for several reasons Maintenance and repairs are difficult to make and required too often The cab is awkward to use Weight distribution is poor because the power unit is on one side and the much lighter husking bed on the other side and the rear end is too light for effective 4-WD Trash build-up makes the engine susceptible to fife and the rigid hitch makes wagon hook-up difficult My combine-equipped picker outperforms the Uni-Harvester in several respects The cab is much more comfortable to operate the drive train is more reliable and the engine is far less susceptible to fire An opening between the husking beds provides total access to every bearing belt and chain The 10-year-old 737 husking beds are more reliable than the Uni-Harvester s newer 838 and 839 husking beds My husking beds produce cleaner corn because I equipped them with fans that blow trash through the husking bed rollers and onto the ground I also built a telescoping lateral-adjustable hitch that can be moved 18 in to either side and pulled out 5 ft making hook-up easy The machine is equipped with three 12-in cross augers One auger moves ears from the feederhouse into the husking bed One auger moves trash from the husking bed s rollers into the front of the sheller The third auger moves ears from the husking beds into the elevator There are four hydraulic pumps - the main pump to raise and lower the header one pump to power the header one to operate the elevator and the combine s hydro-static drive pump McGill removed the cylinder and con-cave and everything behind them except for the bottom frame rail He extended the frame 62 in and replaced the combine s rear axle with a front axle salvaged from a cement truck To power the axle for 4-WD operation he installed a hydraulic motor removed from an International 915 hydrostatic drive combine The new axle operates just like a Mud Hog system at a fraction of the cost and can carry a much heavier load than the Uni-Harvester says McGill Eventually I ll mount 18 4 by 26 lugged combine tires on it The rig s improved weight distribution allows much better 4-WD than the slight assist of the rear wheels offered by Uni-Harvesters The next step was to weld a 6 by 10-ft box beam across the main frame just be-hind the front drive wheels to support the front of the husking beds A shorter box beam supports the rear of the b
To read the rest of this story, download this issue below or click
here to register with your account number.