1983 - Volume #7, Issue #6, Page #02
[ Sample Stories From This Issue | List of All Stories In This Issue | Print this story
| Read this issue]
This Iowa Farm Still Makes, Burns Alcohol
![]() |
![]() |
Robert Spereslage, Greeley, spent some $30,000 a couple years ago to build his still, which he designed after attending seminars on alcohol fuel production and talking with other farm alcohol brewers. Since then he has continued to burn alcohol on his farm, even though there's no longer much information available or interest in doing so. In order to burn the alcohol ù he uses 100 proof ù he had to convert his vehicles himself.
"We didn't want to make a lot of modifications and felt commercial conversion systems on the market were too complicated," says Spereslage. He made two systems, one for gas engines and the other for diesels.
The alcohol converter in his Ford F-150 6 cyl. pickup consists of a Lasso chemical can mounted horizontally near the front of the engine compartment under the hood. An air pipe runs from outside the top of the can to near the bottom of the can. A small tube runs out the top of the can, through a simple turn-on valve and to the air intake valve below the carburetor. When the turn-on valve ù operated from the driver's seat ù is open, air is pulled through the small tube from the can where it has been pulled down through the alcohol and back up again, picking up alcohol vapors. As soon as the valve is opened, and the alcohol vapors start entering the engine, Spereslage says the engine quickly increases its speed by 700 rpm's.
The truck alcohol system burns 2 gal. of alcohol for every 20-gal. tank of gas and boosts mpg 20 to 25%. He notes that the can is filled with metal shavings so the alcohol won't spash around. The entire system costs just $5 for the water turn-on valve. He replaces the Lasso can occasionally due to rust.
To power his Massey Ferguson 175 diesel-powered 63 tractor, Spereslage simply mounts a small tank on the driver's platform, runs the alcohol through a filter, and then up to a tight copper coil which he strapped to the exhaust manifold. The heat from the manifold heats up the coil, which pulls alcohol up from the can and passes it up out of the coil to an inlet in the intake manifold just above. In order to distribute the alcohol vapors evenly to the cylinders on the tractor, he inserted a small copper pipe "manifold" inside the engine manifold housing. The pipe has a small pin prick hole by each of the cylinders so the vapor is released by each cylinder and is therefore burned evenly by each.
Spereslage says the tractor now uses 1 gal. of alcohol for every 2 gal. of diesel fuel. He says total fuel usage was cut from 3 gal. per hour to 2 gal. per hour and the engine horsepower was boosted 4 hp.
Spereslage makes alcohol in his still for about 40 cents a gallon. Figuring diesel fuel at $1.00 a gal., he figures he cut his fuel costs on his diesel by 40% or more. "And I get 4 extra horsepower," he says.
For more information, contact: FARM SHOW Followup, Robert Spereslage, Box 27, Greeley, Iowa, 52050 (ph 319 925-2627).
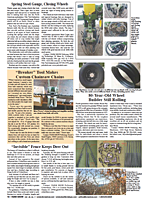
Click here to download page story appeared in.
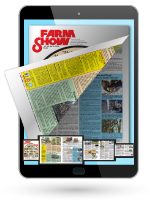
Click here to read entire issue
To read the rest of this story, download this issue below or click here to register with your account number.