You have reached your limit of 3 free stories. A story preview is shown instead.
To view more stories
To view more stories
SUBSCRIBE OR RENEW NOW
(If your subscription is current, click here to Login or Register.)1983 - Volume #7, Issue #5, Page #21
[ Sample Stories From This Issue | List of All Stories In This Issue]
Compressed Air Powers This Conventional Auto
We've heard stories for the past couple years about an inventor in Florida who has figured out a way to run conventional internal combustion engines on compressed air.Now, thanks in part to a report by a freelance writer in "On Magazine", we've received further details and photos of the air-powered car invented..........
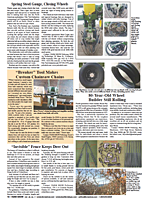
You must sign in, subscribe or renew to see the page.
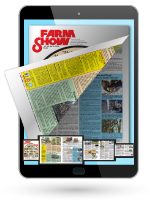
You must sign in, subscribe or renew to see the flip-book
Compressed Air Powers This Conventional Auto ENERGY Alternative Fuels We ve heard stories for the past couple years about an inventor in Florida who has figured out a way to run conventional internal combustion engines on compressed air Now thanks in part to a report by a freelance writer in On Magazine we ve received further details and photos of the air-powered car invented and patented by Leroy K Lee Rogers a Ft Meyers Fla building contractor Rogers who was inundated after early reports on his invention by crowds of reporters manufacturers potential investors and the just plain curious has apparently gone underground Rogers began work on the air car in his garage in 1979 trying to find a reliable way to feed compressed air to conventional gas engine pistons His first car was an 8-cyl 318 cu in 1977 Dodge Aspen wagon Rogers stripped the car of its radiator fuel pump carburetor spark plugs and exhaust system He replaced the engine s carburetor with a distribution block a rectangular hollowed-out aluminum box that channels compressed air to each of the eight cylinders Special valves replaced the spark plugs and the hole where the fuel pump had been attached to the engine was plugged All emission control devices were scrapped and the entire exhaust system was replaced with inexpensive plastic PVC pipe Glynn Wiggins Hendersonville Tenn is an instructor of auto mechanics who recently received his doctorate in auto mechanics education at the University of Tennessee He s seen the converted car and helped Rogers iron out some of the bugs in the system The engine makes almost no noise Exhaust air is actually cooled as it s exhausted because of the sudden drop in pressure which is how refrigeration systems work The day I was there the outside temperature was 80 to 85? while the engine exhaust temp was 40 to 50? Wiggins told FARM SHOW The engine is also very powerful I can kill the engine in my own 400 cu in Pontiac by putting my hand over the exhaust pipe but I couldn t even hold my hand over the exhaust on the air-powered engine When the car went for its first test drive it accelerated so fast it lifted the front wheels of the car off the ground Here s how Lee Rogers described the experience of driving his air car to On Magazine : The difference in driving an air car and a conventional one can be compared with the difference in changing from an automatic to manual transmission The driver has new sensations to deal with but basically that s all One adjustment is in the acceleration In order to gain speed in a gas-powered car you have to put the gas pedal halfway to the floor With the air car it only takes a foot movement of a quarter inch The acceleration rate is instantaneous The engine works on just 80 lbs of air pressure Rogers removed the gas tank and replaced it with three small tanks about the size of pressurized-carbonated beverage containers that ll hold 2 to 3 cu ft of air A key feature of the air system is that it takes in a tremendous amount of outside air ù about a 20 to 1 ratio to the pressurized air ù and recaptures the pressurized exhaust air in the air storage tanks In other words Rogers says the car pressurizes enough air on the go to help power itself and require less refilling The system has to recapture 1/ 20th of the air passing through the engine One of the problems left in developing a marketable kit that ll install on any engine is that the blower used to recapture pressurized air off the engine is too efficient It needs to be down-sized to capture only as much air as is needed Wiggins explains Rogers starts the engine with the car s electric starter and then opens the throttle or air supply lines After 3 to 5 min of operation the exhaust is actually cool to the touch The engine is simple powerful quiet running and has low maintenance requirements I detected no contradictions to the inventor s claims It went far beyond my expectations Wiggins told FARM SHOW The air-powered engine conversion kit reportedly will work on any gas-powered engine Rogers has already installed his second conversion kit in a 4-cyl Chevrolet Vega engine The idea may also work in diesel engines but since they operate at higher pressures and don t have spark plugs a different approach would have to be taken Wiggins syas the biggest roadblock to getting the Roger s conversion kit - which has been designed to cost $1 000 to $1 500 - into production has been a lack of funds to finish testing He has had many offers of money but everyone wants to buy the invention outright He figures it would never get on the market if he did that So he has continued to finance all research and development on his own There s no doubt the technology is there but it will take time to put everything together says Wiggins
To read the rest of this story, download this issue below or click here to register with your account number.