You have reached your limit of 3 free stories. A story preview is shown instead.
To view more stories
(If your subscription is current,
click here to Login or Register.)
Pivoting Shop Crane
A 14 ft. high, 18-ft. long crane that pivots 180? from side to side and is equipped with a 2-ton hoist lets Albert Harder, Butterfield, Minn., reach up to 12-ft. outside his shop to bring heavy equipment inside.
Harder used two 12-in. I-beams, 5-in. wide, to build the crane, removing one beam from an old bridge
..........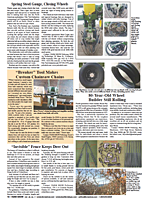
You must sign in, subscribe or renew to see the page.
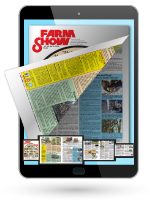
You must sign in, subscribe or renew to see the flip-book
Pivoting shop crane FARM SHOP Maintenance 13-4-10 A 14 ft. high, 18-ft. long crane that pivots 180? from side to side and is equipped with a 2-ton hoist lets Albert Harder, Butterfield, Minn., reach up to 12-ft. outside his shop to bring heavy equipment inside.
Harder used two 12-in. I-beams, 5-in. wide, to build the crane, removing one beam from an old bridge and the other from an old fertilizer plant. The beams pivot freely on tractor axle shafts mounted in the ceiling and floor. To swing the crane, Harder simply grabs onto the dolly hoist and pulls.
"The pivoting crane is one of the handiest tools in my shop," says Harder. "It lets me pick up something outside the shop, such as a sprayer cab, and swing it into the shop. It's much more convenient than a floor hoist because there are no legs in the way, and it's much safer than a tractor loader because of its stability."
Harder reinforced the ceiling to support the weight of a framework that anchors a 2-ft. long, 3-in. dia. cut-down axle shaft from a Farmall F-12. He used a tractor loader to lift the beams into place and then welded the ends together and braced the corner joint with a 4-in. dia. brace pipe. Using a cutting torch, he cut an 18-in. deep, 3-in. dia. hole through the top of the horizontal beam and down into the vertical beam. Then he slipped the axle shaft down through the ceiling and into the hole, and welded it to the beam. He in-stalled another axle shaft and bearing in the floor below the vertical beam.
Contact: FARM SHOW Followup, Albert Harder, Rt. 1, Box 194, Butter-field, Minn. 56120 (ph
To read the rest of this story, download this issue below or click
here to register with your account number.