1993 - Volume #17, Issue #4, Page #09
[ Sample Stories From This Issue | List of All Stories In This Issue | Print this story
| Read this issue]
Mulch Finisher Modified To Solve Ridging Problem
Steve Warters wasn't happy with his 1984 Deere 722 mulch finisher because it left big ridges. The Tuscola, Ill., fanner solved the problem by changing the angle of the disk gangs and reversing the position of the disk blades on each gang.The mulch finisher was equipped with four sets of disk gangs in front followed by cultivator sweeps and a harrow. Each gang was factory set at a 9 degree angle to the frame. Waiters reversed the direction of the disk blades so they would pull soil in toward the center of the tillage tool instead of pushing it out. He did it by swapping blades on the left side of each gang with the blades on the right side, moving the left outside blade to the right outside position, the second-to-left blade to the second-to-right position, and so on. He also changed the angle of each gang from 9 to 7 degrees by cutting apart the frame and moving one end of the gang slightly backward.
"As originally built it was a very poor tillage tool because it tended to push soil out past the cultivator sweeps, leaving big ridges with no way to level them out," says Warters. "I've used this modified rig over a lot of ground. It works so well that three other farmers asked me to modify their mulch finishers the same way. I made the changes after I found out my dealer wanted $12,500 - plus my old disk - to trade up to a new model. I figured I could make a lot of mistakes with my welder for that much money. Deere later came out with a model similar to mine, but it's not built as heavy."
Reversing the direction of the disk gangs left a 16 in. wide untilled strip at the center of the tillage tool. To solve the problem, Warters bolted a pair of disk hillers (designed for a Buffalo ridge till cultivator) under the hitch at the center of the frame. The disk killers are bolted to a steel plate that bolts to the frame. Depth can be easily adjusted as needed.
He also modified the mulch finisher's self-leveling hitch by lengthening the pivot assembly so that the harrow won't drag on the road. He welded a pair of 1/2-in. thick steel plates onto the hitch to move the pivot point 4 in. farther back. "The problem was that if the hitch was level in field position, the mulch finisher tilted rearward on the road which caused the harrow to drag. Now the mulch finisher stays level whether it's up or down," notes Warters.
Contact: FARM SHOW Followup, Steve Warters, Box 198, Tuscola, Ill. 61953 (ph 217 253-4530).
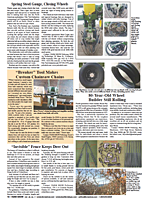
Click here to download page story appeared in.
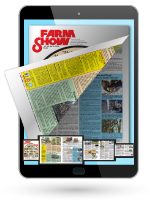
Click here to read entire issue
To read the rest of this story, download this issue below or click here to register with your account number.