You have reached your limit of 3 free stories. A story preview is shown instead.
To view more stories
(If your subscription is current,
click here to Login or Register.)
Wooden Basements Catching On Fast
If you're planning to build a new home, you'll want to check into the possibility of using treated wood instead of poured concrete or blocks for the basement walls or foundation. Treated wood also is worth looking into if you're looking for a longlasting pit for storing liquid manure.
Big reasons behind the boom
..........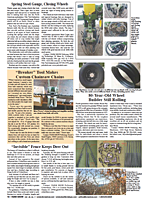
You must sign in, subscribe or renew to see the page.
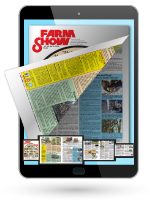
You must sign in, subscribe or renew to see the flip-book
Wooden Basements Catching On Fast FARM HOME Houses 1-3-20 If you're planning to build a new home, you'll want to check into the possibility of using treated wood instead of poured concrete or blocks for the basement walls or foundation. Treated wood also is worth looking into if you're looking for a longlasting pit for storing liquid manure.
Big reasons behind the boom in wooden basements, according to industry officials FARM SHOW contacted, is that they're drier, better insulated and easier and less costly to install than conventional concrete or blocks. What's more, wooden walls will support as much weight as concrete, and they last just as long if not longer. They're also easier to wire and finish, and they offer a lot more flexibility in design.
"On a 3-bedroom home, you can save several hundred dollars with a wooden foundation," says Leonard Lokey, marketing manager for the Southern Divison of Osmose, a leading supplier of treated wood, at Griffin, Ga. "Virtually all building codes now endorse treated wooden foundations and they're catching on fast clear across the U.S.".
A popular new wrinkle is to install treated wood basement floors along with wooden walls. Wooden floors are warmer than bare concrete and easier to keep up. At present, most city codes require that a concrete floor be poured under the wooden floor to act as a support to keep the walls aligned. In Canada, however, many homes are reportedly being built with wooden basement walls and wooden floors - without any concrete underneath.
The Osmose Company uses a new K-33 wood preservative, applied under pressure, to treat Wood. The chemical preservative is pressure impregnated deep into the cellular structure of the wood and is permanently locked into the wood. Strength of the wood is not affected by treating.
Here's how professional home builders from all corners of the U.S. size up what the building industry refers to as All-Weather Wood Foundations (AWWF):
Ohio: "The AWWF is strong. It has warmth. The last one I built - mine - saved $300 to $400 over the cost of concrete blocks or poured concrete walls." Dick Wolfe, Kingswood Lumber Co., Columbus.
California: "We've found that the AWWF basement costs about two thirds as much as the concrete-block type in multi-level homes, and it cuts construction time by about five days." Cliff Cheney, Stone Brothers and Associates, Modesto.
Indiana: "Although costs in the Indianapolis area are about the same for wood and conventional foundations, you can't get around the savings of time- five to six hours versus days." Stephen Davidson, Stephen Davidson Associates, Greenwood.
Wisconsin: "Our sales department has found that once customers see and understand the wood foundation, that is the system they demand. It's far more saleable than a masonry foundation." Charles Bull, Neitzel Construction, Onalaska.
Minnesota: "We started building wooden foundations 6 years ago. About 98% of our installations are outstate, mostly in rural areas. We use 1/2 in. treated plywood and run the sheets horizontally for more strength. Does the same job as 3/4 in. sheets and costs a lot less. On a 30 by 50 ft. home, the entire basement installation - starting with bare ground - can be completed in a day." Peter White, Manager, Shaw Lumber, St. Paul, Mn.
For more details, check with your nearest lumber yard. Ask for literature on wooden basements and foundations, including tips for do-it-yourself installation. Brochures on the fast-growing new procedure are also available from the following sources:
American Wood Preservers Institute, 165101d Meadow Rd., McLean, Va. 22101.
National Forest Products Association, 1619 Massachusetts Avenue NW, Washington, D.C. 20036. Ask for "The All-Weather Wood Foundation System; Design, Fabrication and Installation Manual."
American Plywood Associates, 1119 A Street, Tacoma, Wash. 98401 (ph, 206 272-2283). Ask for the brochure, "The All-Weather Wood Foundation: Why, What and How". They also offer a brochure on "Plywood Liquid Manure Storage Tanks."
Osmose Wood Foundations, 980 Ellicott St., Buffalo, N.Y. 1420
To read the rest of this story, download this issue below or click
here to register with your account number.