1993 - Volume #17, Issue #1, Page #19
[ Sample Stories From This Issue | List of All Stories In This Issue | Print this story
| Read this issue]
Minnesota Farmer Builds Wooden-Gear Clocks
![]() |
Meyer uses ordinary tools, including a band saw and drill press, to make the clocks. He uses veneer plywood for the gears and hard maple for the gear supports. Clocks mount on vertical chrome tubes.
"People are impressed when they see them, but most can't figure out how they work," says Meyer, of Elgin. "Wooden gear clocks date back to the 1700's. However, today very few people know how to build them. I got started four years ago after I read a story in a wood working magazine that described how wooden clocks work. It showed how to make the `Thomas clock' which has been around for 30 years. I tried making it but wasn't satisfied with the plans so I made my own design.
"The story said wooden clocks could be built only by advanced woodworkers, but I found that isn't true. However, it does re-quire precision work. There are 120 teeth on the center wheel and each of them has to be cut at an exact 3 degree angle. The escapement wheel and lever also have to be cut perfect. The most difficult part is getting everything square when cutting holes for the gear shafts. There can't be any wobble in the gears or they'll skip or bind. I've built 22 clocks so far but have sold only four of them to neighbors and friends. I burned up the rest because I wasn't happy with the overall design.
"Building wooden clocks is a great hobby because it doesn't take a lot of money or equipment to get started. I use a band saw to cut the teeth and to make the gear supports. I use a drill press to make holes for the shafts. If I push hard, I can make a clock in two days."
Wooden clocks are weight-driven. Meyer builds the weights by cutting off sections of 5-in. dia. chrome exhaust pipe designed for semi tractors and filling them with lead shot. The weights are mounted on a pulley that's connected to the center wheel. A crank mounted behind the center wheel is used to pull the weights up.
The heart of the clock is the center wheel which is connected to a timing gear that divides minutes and hours. The weights drive the center wheel which goes around once an hour, driving an escapement wheel that drives the pendulum.
"It takes 30 hours for the weights to fall to the floor. That's the maximum time between windings for wooden clocks because they can't be geared down like grandfather clocks. There's too much friction between the gears," says Meyer, noting that his wooden clocks are accurate to within 1 or 2 min. between windings.
Meyer says he's willing to sell his latest clock (shown) for $500. He's now working on a larger clock that will be 9 ft. tall, 6 ft. wide, and 4 ft. deep. It'll have a 4-ft. dia. center gear wheel. He has made up detailed plans for his first clock and will have other plans available early next year.
For more information, contact: FARM SHOW Followup, Bob Meyer, 7347 Hwy. 247 N.E., Elgin, Minn. 55932 (ph 507 876-2484).
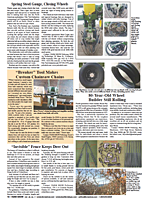
Click here to download page story appeared in.
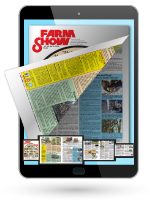
Click here to read entire issue
To read the rest of this story, download this issue below or click here to register with your account number.