You have reached your limit of 3 free stories. A story preview is shown instead.
To view more stories
(If your subscription is current,
click here to Login or Register.)
Double Toolbar Rotary Hoe Controls Weeds In The Rows
Marvin Manges, Yale, Ill., turned his 29 1/2-ft. wide Deere rotary hoe into a 19 1/2-ft., 8-row "double toolbar" hoe that he uses to control in-row weeds in his 30-in. spaced corn.
"It has twice as much soil mixing action as a conventional rotary hoe, allowing me to eliminate weeds within the row without using he
..........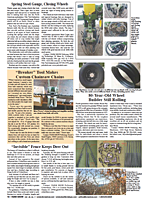
You must sign in, subscribe or renew to see the page.
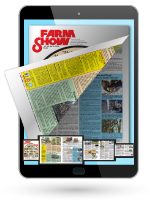
You must sign in, subscribe or renew to see the flip-book
Double Toolbar Rotary Hoe Controls Weeds In The Rows CROPS Weed Control 18-5-9 Marvin Manges, Yale, Ill., turned his 29 1/2-ft. wide Deere rotary hoe into a 19 1/2-ft., 8-row "double toolbar" hoe that he uses to control in-row weeds in his 30-in. spaced corn.
"It has twice as much soil mixing action as a conventional rotary hoe, allowing me to eliminate weeds within the row without using herbicides," says Mange.
Manges farms organically, using no chemicals or commercial fertilizer. He plants all his crops on ridges and uses cover crops to control weeds. He uses the same traffic pattern to plant, rotary hoe, cultivate, and chop stalks. He uses a Buffalo shredder to chop stalks and mulch cover crops and 14-in. wide Buffalo sweeps on his 8-row planter to level the ridges. He uses a Buffalo cultivator to control weeds between rows.
He cut 10 ft. off one end of the toolbar and welded it to a 9 1/2-ft. long 4 by 6 steel bar, then welded in steel cross beams and end plates to connect the two toolbars together. The toolbars are 26 in. apart. He remounted the hoe wheels in groups of four spaced 30 in. apart on each toolbar, with the wheels in each group spaced 3 in. Each front group of hoe wheels is offset 3/4 in. to the left of the center of the row and each rear group is offset 3/4 in. to the right of the row center so that the wheels are spaced evenly across the row, with 1 1/2 in. gaps between them.
A pair of depth gauge wheels mounts on the front toolbar to control depth of the front hoe wheels. Depth of the rear gangs is controlled by the top link on the 3-pt. hitch.
"It gives me the benefits of going over the field twice with just one pass," says Mange. "Because I don't use any herbicides my biggest problem is controlling weeds in the row. I use the rotary hoe before planting to `peel' off the top of the ridge. It provides a clean surface for planting. I use it again every third or fourth day after planting until corn is in the four or five-leaf stage and big enough to cultivate. I adjust hoe wheel depth for each pass depending on crop stage and soil conditions. I set the depth gauge wheels first, then use the 3-pt. to adjust the rear hoe wheels up or down.
"One advantage is that my double toolbar rotary hoe has only 64 wheels compared to the original 96 wheels so there's about 50% more down pressure per wheel, not including the weight of the extra toolbar, cross beams, and end plates. The extra weight really helps in hard soil conditions.
"After shortening the toolbar I recentered the 3-pt. hitch. To ensure that the hoe pulls straight, I mounted the rotary hoe wheels on the left side of the rear toolbar 3/4 inch to the left of the front four wheels, and the wheels on the right side of the rear toolbar 3/4 inch to the right of the front four wheels."
To weld the two pieces of the rear toolbar together, Mange welded two lengths of 1/2-in. dia. steel rod Onto one end of each toolbar at opposite corners, allowing the toolbars to slip inside each other so they would stay in place before he did the final welding.
The hoe wheel mounting arms pivot on the original 1-in. dia. lengths of shaft. Mange cut the shafts down to fit the new wheel positions and used 2-in. sq. steel tubing to make mounting brackets for them. J-bolts through the tubing are used to secure the shafts.
Contact: FARM SHOW Followup, Marvin Manges, Rt. 1, Box 49, Yale, Ill. 62481 (ph 618 793-2060).
To read the rest of this story, download this issue below or click
here to register with your account number.