You have reached your limit of 3 free stories. A story preview is shown instead.
To view more stories
(If your subscription is current,
click here to Login or Register.)
Calving Shed Made From Straw Bales
"It keeps newborn calves `toasty warm,' even when outside temperatures reach 20? below zero," says Alma Hubbard, Grace, Idaho, of his low-cost calving shed made of straw bales and plastic. The 70 by 32 ft. shed features a clear plastic roof and straw-bale sidewalls. "It's almost three years old and has proved to be dur
..........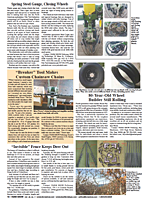
You must sign in, subscribe or renew to see the page.
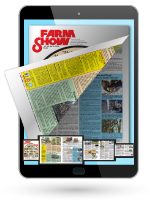
You must sign in, subscribe or renew to see the flip-book
Calving shed made from straw bales LIVESTOCK Buildings 11-6-16 "It keeps newborn calves `toasty warm,' even when outside temperatures reach 20? below zero," says Alma Hubbard, Grace, Idaho, of his low-cost calving shed made of straw bales and plastic. The 70 by 32 ft. shed features a clear plastic roof and straw-bale sidewalls. "It's almost three years old and has proved to be durable," says Hubbard. "It even made it through a tornado."
Forming the shed's walls are 55 one-ton rectangular 4 by 4 by 8 ft. straw bales. The walls are three bales high in front (north side) and two bales high in back (south side). There's a 12 ft. wide walkway along the north side, and a 3 ft. walkway on the other three sides, with six pens , each 10 ft. square, between the walkways.
The stalls are arranged far enough away from the bales so that cows won't eat the walls. Two doors provide cross ventilation. Gaps between the bales let heat escape and help keep humidity at optimum levels to minimize condensation. The dirt floor is covered with straw and the plastic roof provides warmth during cold weather. It's made of two layers of 8 mil clear, heat shrink plastic, and is slanted to shed snow and rain. "The clear plastic absorbs sunlight and heat during the day and radiates it back out at night," says Hubbard. "The shed's main benefit is that it gets calves off to a fast, healthy start. As soon as calves are dropped outside, we bring them and the mother cow into the shed and keep them there for 12 to 24 hours," explains Hubbard. "We make sure calves get that first colostrum milk, eartag them and give them 7-way and vita-min shots."
Hubbard estimates the shed's construction cost at about $2,300. That includes $825 for the 55 straw bales ($15 per bale); $1,000 for the roof (double layers of clear plastic); and $475 for lumber and labor. "With a conventional calving shed, it's likely that you couldn't put in a cement foundation for $2,300. Besides, when we tear down someday, we can reuse the lumber and convert the straw to bedding. I
expect it to last another five years with very little maintenance."
To make the roof, Hubbard wrapped double layers of 8 mil clear plastic around the 2 by 6 in. rafters, then heated the heat-shrink plastic with a propane torch which caused the inside and outside layers to stick to each other and tighten up. There's no sagging between the 2 by 6's and the plastic, which has never ripped., says Hubbard.
The shed is designed so he can pull out and replace the straw bales, or even expand the structure up to twice its size. He's convinced that straw and plastic could be used to economically make other farm buildings, such as a greenhouse or garage.
For more information, contact: FARM SHOW Followup, Alma Hubbard, Rt. 1, Box 230., Grace, Idaho 83241 (ph 208 425-3366).
To read the rest of this story, download this issue below or click
here to register with your account number.