Maryland Farmer Builds Round Bale Wrapper
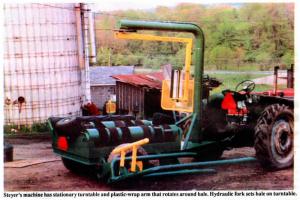 ✖  |
Most bale wrap machines have a rotating turntable and a stationary arm that unrolls plastic to wrap the bale as it turns. A Mary-land farmer who didn't like that bale wrap design has built a new-style machine with a stationary turntable and a plastic-wrap arm that rotates around the bale.
"It'll outwrap any bale wrapper on the market because it solves the problem of bales falling off the rotating turntable, and because it can be used on both wet and dry bales, doing the work of two machines," says Randall Steyer, Oakland, Md.
Mounted on a two-wheel trailer, the machine picks the bale off the ground with a hydraulic fork and sets it on the turntable. A pair of belted rollers on the table turn the bale slowly, while the plastic-wrap arm rotates 360? around it. After the bale has been wrapped, a hydraulic cylinder tilts the table to one side to dump the bale off. To put a sleeve on a lower moisture bale that leaves the ends open, the plastic-wrap arm is positioned horizontally above the bale, then the arm swings forward and back along the length of the bale as it turns.
"I've used it to wrap over 2,000 bales with virtually no problems," says Steyer, who built the bale wrapper two years ago. "I've even used it to wrap bales for many of my neighbors who had trouble with bales falling off their bale wrap machines. The problem is that when bales get lopsided or oblong they can easily fall off the table as it rotates. Another problem is that with a very lopsided bale the belts often slip. The bale stops rolling but the turntable continues to rotate, causing layer after layer of plastic to cover the same place on the bale. I can stop the rotating arm independent of the rollers to avoid wasting plastic. I can also independently control speed of the rollers and rotating arm according to bale size.
"I built it for $2,000. Commercial bale wrappers cost at least $12,000."
Steyer used channel iron and steel sheeting to build the trailer frame which he mounted on a mobile home trailer axle. The 15-in. tires are off an old pickup. He used 6-in. dia. steel tubing to make the overhead support arm and 3-in. dia. steel tubing to make the side-mounted bale fork. Two small rubber wheels (taken from an ATV) and a rubber side bumper (from an old New Holland 404 hay conditioner), keep bales from falling off the table. The steel rollers on the table also come from the New Holland 404 hay conditioner.
Two hydraulic cylinders are used to lift the bale onto the table. Another cylinder is used to lift the table and dump the bale off. The rotating arm is chain-driven by a hydraulic motor. Another hydraulic motor is used to turn the rollers. Control levers mount behind the tractor seat. "I generally operate the control levers from the ground because I have to get off the tractor anyway to tie the plastic onto the bale and to cut it after the bale is wrapped," notes Steyer.
For more information, contact FARM SHOW Followup, Randall Steyer, Rt. 3, Box 8075, Oakland, Md. 21550 (ph 301 334-2900).
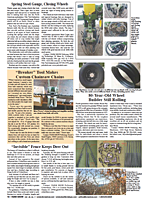
Click here to download page story appeared in.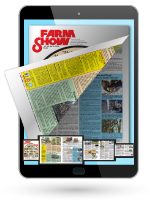
Click here to read entire issue
Maryland Farmer Builds Round Bale Wrapper HAY & FORAGE HARVESTING Bale Handling (5) 17-2-15 Most bale wrap machines have a rotating turntable and a stationary arm that unrolls plastic to wrap the bale as it turns. A Mary-land farmer who didn't like that bale wrap design has built a new-style machine with a stationary turntable and a plastic-wrap arm that rotates around the bale.
"It'll outwrap any bale wrapper on the market because it solves the problem of bales falling off the rotating turntable, and because it can be used on both wet and dry bales, doing the work of two machines," says Randall Steyer, Oakland, Md.
Mounted on a two-wheel trailer, the machine picks the bale off the ground with a hydraulic fork and sets it on the turntable. A pair of belted rollers on the table turn the bale slowly, while the plastic-wrap arm rotates 360? around it. After the bale has been wrapped, a hydraulic cylinder tilts the table to one side to dump the bale off. To put a sleeve on a lower moisture bale that leaves the ends open, the plastic-wrap arm is positioned horizontally above the bale, then the arm swings forward and back along the length of the bale as it turns.
"I've used it to wrap over 2,000 bales with virtually no problems," says Steyer, who built the bale wrapper two years ago. "I've even used it to wrap bales for many of my neighbors who had trouble with bales falling off their bale wrap machines. The problem is that when bales get lopsided or oblong they can easily fall off the table as it rotates. Another problem is that with a very lopsided bale the belts often slip. The bale stops rolling but the turntable continues to rotate, causing layer after layer of plastic to cover the same place on the bale. I can stop the rotating arm independent of the rollers to avoid wasting plastic. I can also independently control speed of the rollers and rotating arm according to bale size.
"I built it for $2,000. Commercial bale wrappers cost at least $12,000."
Steyer used channel iron and steel sheeting to build the trailer frame which he mounted on a mobile home trailer axle. The 15-in. tires are off an old pickup. He used 6-in. dia. steel tubing to make the overhead support arm and 3-in. dia. steel tubing to make the side-mounted bale fork. Two small rubber wheels (taken from an ATV) and a rubber side bumper (from an old New Holland 404 hay conditioner), keep bales from falling off the table. The steel rollers on the table also come from the New Holland 404 hay conditioner.
Two hydraulic cylinders are used to lift the bale onto the table. Another cylinder is used to lift the table and dump the bale off. The rotating arm is chain-driven by a hydraulic motor. Another hydraulic motor is used to turn the rollers. Control levers mount behind the tractor seat. "I generally operate the control levers from the ground because I have to get off the tractor anyway to tie the plastic onto the bale and to cut it after the bale is wrapped," notes Steyer.
For more information, contact FARM SHOW Followup, Randall Steyer, Rt. 3, Box 8075, Oakland, Md. 21550 (ph 301 334-2900).
To read the rest of this story, download this issue below or click
here to register with your account number.