You have reached your limit of 3 free stories. A story preview is shown instead.
To view more stories
(If your subscription is current,
click here to Login or Register.)
Self-Propelled Baler
"It's more maneuverable, visibility is great, and it frees up a tractor for other work," says Clarence Stonebrink, Enterprise, Ore., who combined a Vermeer round baler and a Hesston swather to produce a slick new first-of-its-kind self-propelled big round baler.
Stonebrink, along with his sons Don and Glen, bales
..........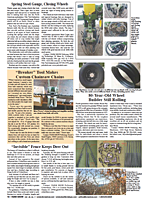
You must sign in, subscribe or renew to see the page.
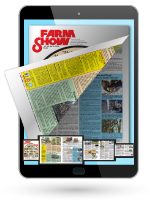
You must sign in, subscribe or renew to see the flip-book
Self-Propelled Baler HAY & FORAGE HARVESTING Balers (6) 9-2-1 "It's more maneuverable, visibility is great, and it frees up a tractor for other work," says Clarence Stonebrink, Enterprise, Ore., who combined a Vermeer round baler and a Hesston swather to produce a slick new first-of-its-kind self-propelled big round baler.
Stonebrink, along with his sons Don and Glen, bales 300 to 400 acres of hay each year. "Our new baler gets the job done faster and easier than ever before. It turns around in its tracks so you don't have to drive around in circles or make big turns to pick up lost hay, as with a pull-behind baler. If you slip off the windrow you can instantly make adjustment so almost no hay is lost."
The match-up of the 12-year-old Hesston 620 swather and the new Vermeer 504 baler was a natural because the swather is equipped with both hydrostatic and mechanical drives needed for ground drive and operation of the baler.
Stonebrink stripped the header, and all other unnecessary metal and parts, off the swather. A piece of 4 by 4-in. steel tubing mounts at a right angle to the left side of the swather drive unit and runs under the baler to a hydrostatically-driven wheel on the other side of the baler. The baler is pinned to pivot points on top of the steel beam that allow it to pivot up and down so hay pick-up height can be adjusted. Metal braces that attach
to the front of the baler hold it in place once height is adjusted. Controls on the swather drive unit were reversed to travel in the opposite direction. The baler can be quickly removed and converted back to a pull-type, if needed, since it's not modified in any way. Wheels and tongue were simply unbolted and removed.
Both the drive wheel on the swather and the baler-mounted wheel are hydrostatically driven. A driveshaft on the swather drive unit, which was originally used to power the swather header, runs to a right angle gearbox on the baler ù originally driven by a tractor pto ù to provide power for baling.
The two machines make for an ideal match-up both because of the combination of mechanical and hydrostatic drive and because the swather was an end-drive unit. "The drive units on most new swathers are mounted in the center of the machine and may not work as well as this machine for mounting off to the side of the baler," Stonebrink points out.
The unique self-propelled baler has been in use for two seasons. "It's much faster than baling with a tractor and baler. You can quickly pick up hay in odd-shaped corners and make square corners on windrows. If you slip off the row you can just back up and pick it up. Visibility is also good because the operator sits right alongside the baler. You can see the windrow without constantly turning around and, when tying, you can easily see the twine. When you've finished a field, you just pull a lever on the baler and go. The unit has a road gear for speedy travel to the next field," explains Stonebrink.
The swather was painted Vermeer yellow to match the baler. Except for labor, the only real construction cost was for the used swather, which cost around $2,000. While the Stonebrinks are Vermeer dealers, they have no plans to market or build the self-propelled baler.
For more information, contact: FARM SHOW Followup, Clarence Stonebrink, 509 W. Main, Enterprise, Ore. 97828 (ph 503 426-3503).
To read the rest of this story, download this issue below or click
here to register with your account number.