Home-Built 25 Ft Air Reel
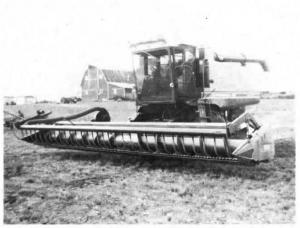 ✖  |
"We built our own 25-ft. air reel for less than half the cost of a new one and it works great, especially in short crops," says custom combiner Bernard Martin, Willow Bunch, Sask., who along with brother Raymond used a Valmar blower to power the air reel. They mounted it in place of the conventional reel on their IH 1460 pull-type combine.
"We needed an air reel last summer because we could see that the crop was going to be short," says Bernard, who notes that the brothers farm about 3,200 acres. "Commercial air reels cost about $3,500, but we built ours for $1,700 and we built it the way we wanted it. It works great in short crops and equally well in tall, heavy crops. We saved 3 to 5 bu. per acre. Any grain that falls onto the cutter-bar is blown into the header. Bat reels work alright in tall crops but in short crops some grain lodges behind the cutterbar and because the straw is so short the batt reels can't reach it. An air reel doesn't need straw to work. We can clip even short crops just below the grain heads. Also, the visibility is great. We can see just as well at night as during the day."
The Martins bought the 18-in. dia. blower and mounted it on the right side of their Case-IH 1010 header. The blower is powered off the sickle drive shaft. They used a series of belts and pulleys to speed up the blower to run at 4,200 rpms and enlarged the blower's throat dia. from 4 to 6 in. to increase air volume. Air goes through a flex-tube into a 25-ft. long, 6-in. dia. steel manifold mounted on the reel arms and out nozzles spaced 10-in. apart (five nozzles in front of the feederhouse are spaced 8 in. apart). The curtain of air pushes the crop into the header. A shroud covers the fan inlet to keep straw and chaff from entering the fan.
The Martins used an oversized sprocket to slow down the feeder auger to make sure it doesn't throw grain heads out in front of the combine. "An air reel has no batts to hold the crop in," notes Bernard.
To make the downspouts, which are curved toward the cutterbar, the Martins cut a 1 1/4-in. dia. hole every 10 in. in the manifold and welded the downspouts in. They welded a 1 by 1/4-in. strip of metal inside the middle portion of the end of each downspout. Then they flattened the end of each downspout and cut it in a V-shape to shorten the sides of the downs-pout tip, ensuring complete air coverage between downspouts. "We use a manually-operated pivot to move the manifold back and forth and a hydraulic cylinder operated from the cab to move the manifold up or down," notes Bernard.
Contact: FARM SHOW Followup, Bernard Martin, Box 332, Willow Bunch, Sask., Canada S0H 4K0 (ph 306 473-2616).
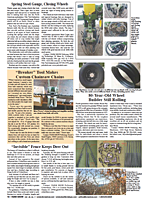
Click here to download page story appeared in.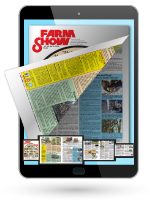
Click here to read entire issue
Home-Built 25 Ft Air Reel COMBINES Conversions 13-5-8 "We built our own 25-ft. air reel for less than half the cost of a new one and it works great, especially in short crops," says custom combiner Bernard Martin, Willow Bunch, Sask., who along with brother Raymond used a Valmar blower to power the air reel. They mounted it in place of the conventional reel on their IH 1460 pull-type combine.
"We needed an air reel last summer because we could see that the crop was going to be short," says Bernard, who notes that the brothers farm about 3,200 acres. "Commercial air reels cost about $3,500, but we built ours for $1,700 and we built it the way we wanted it. It works great in short crops and equally well in tall, heavy crops. We saved 3 to 5 bu. per acre. Any grain that falls onto the cutter-bar is blown into the header. Bat reels work alright in tall crops but in short crops some grain lodges behind the cutterbar and because the straw is so short the batt reels can't reach it. An air reel doesn't need straw to work. We can clip even short crops just below the grain heads. Also, the visibility is great. We can see just as well at night as during the day."
The Martins bought the 18-in. dia. blower and mounted it on the right side of their Case-IH 1010 header. The blower is powered off the sickle drive shaft. They used a series of belts and pulleys to speed up the blower to run at 4,200 rpms and enlarged the blower's throat dia. from 4 to 6 in. to increase air volume. Air goes through a flex-tube into a 25-ft. long, 6-in. dia. steel manifold mounted on the reel arms and out nozzles spaced 10-in. apart (five nozzles in front of the feederhouse are spaced 8 in. apart). The curtain of air pushes the crop into the header. A shroud covers the fan inlet to keep straw and chaff from entering the fan.
The Martins used an oversized sprocket to slow down the feeder auger to make sure it doesn't throw grain heads out in front of the combine. "An air reel has no batts to hold the crop in," notes Bernard.
To make the downspouts, which are curved toward the cutterbar, the Martins cut a 1 1/4-in. dia. hole every 10 in. in the manifold and welded the downspouts in. They welded a 1 by 1/4-in. strip of metal inside the middle portion of the end of each downspout. Then they flattened the end of each downspout and cut it in a V-shape to shorten the sides of the downs-pout tip, ensuring complete air coverage between downspouts. "We use a manually-operated pivot to move the manifold back and forth and a hydraulic cylinder operated from the cab to move the manifold up or down," notes Bernard.
Contact: FARM SHOW Followup, Bernard Martin, Box 332, Willow Bunch, Sask., Canada SOH 4K0 (ph 306 473-2616).
To read the rest of this story, download this issue below or click
here to register with your account number.