You have reached your limit of 3 free stories. A story preview is shown instead.
To view more stories
(If your subscription is current,
click here to Login or Register.)
He Built His Own Combine
"I built my own combine for $10,000, saving about $90,000 on the cost of a comparable new one," says Perry Jensen, Churchbridge, Sask., who merged the threshing mechanism of his 1980 Russian-built Belarus SK-6 combine with the hydrostatic drive axle, 4-speed hydrostatic transmission, tires and rims, unloading auger and
..........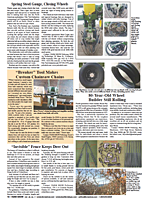
You must sign in, subscribe or renew to see the page.
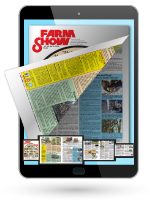
You must sign in, subscribe or renew to see the flip-book
He built his own combine COMBINES Conversions 13-4-2 "I built my own combine for $10,000, saving about $90,000 on the cost of a comparable new one," says Perry Jensen, Churchbridge, Sask., who merged the threshing mechanism of his 1980 Russian-built Belarus SK-6 combine with the hydrostatic drive axle, 4-speed hydrostatic transmission, tires and rims, unloading auger and entire hydraulic system from a wrecked 1977 Gleaner L-2 combine.
"It has all the best features of both the Belarus and Gleaner. We bought the Belarus combine new in 1981 and used it for four years before deciding that we either had to make some changes on it or trade it in," says Jensen. "The V-6 diesel engine was fuel efficient and the combine had good threshing capacity due to the dual 60-in. cylinders, long straw walkers and sieves. However, the clutch and variable 3-speed transmission caused me endless trouble, especially in heavy swaths. It would never travel at the right speed but was always either too fast or too slow. I usually combined in first gear, but in heavy swaths I couldn't slow down so I had to use the clutch constantly, which caused the belts to stretch and the feeder auger to plug up. The gears shifted hard and I couldn't turn sharp enough on corners. In addition to the drive train, we also wanted to improve the hydraulics, unloading auger, grain tank capacity and cab visibility.
"A new Belarus would have cost $100,000 so I decided to rebuild the old one. I paid just $2,650 for a junked Gleaner which was wrecked when it rolled off a semi. Its power train was still intact but was surrounded by crumpled sheet metal and threshing parts. I gambled that the hydrostatic drive and trans-mission would still work, and they did. The new drive train alone solved so many problems in heavy swaths that I can hardly believe I'm using the same combine. Now I usually combine in third gear, and can slow down to a crawl in every gear except fourth. The hydrostatic transmission is also more fuel efficient and uses less horsepower than the Belarus transmission."
To install the new hydrostatic drive, Jensen pulled out the Belarus drive train and reversed the tires and rims on the Gleaner axle which added 10 in. of clearance to allow it to fit under the Belarus. He bolted a 6-in. I-beam along the top of the axle in order to keep the combine at the proper height. The Belarus transmission was driven off the right side of the combine, but the Gleaner transmission was driven off the left side. To solve the problem, Jensen installed a belt-driven shaft which runs from the engine through the cleaning fan's air chamber to the hydrostatic transmission. He also installed the Gleaner's hydraulic system using the original oil pump, reservoir and cylinders. "The Belarus hydraulic system worked at low pressure, causing the steering and header lift systems to work slowly. The Gleaner's hydraulic system uses high pressure so it responds much faster," notes Jensen.
The next step was to install the Gleaner's swing-down unloading auger. "The unloading auger on the Belarus was so low it just cleared our tandem grain truck;' says Jensen. "The Gleaner's swing-down unloading auger easily reaches over the truck. Also, we couldn't turn sharp enough on corners so we installed the Gleaner's hydraulic steering cylinder which has a longer stroke than the Belarus. We also placed the tie rod on the other side of the axle, making it possible to turn a 90? corner without using the wheel brakes."
Next, Jensen went to work rebuilding the Belarus cab, substituting the Gleaner's floor pan, seat, and overhead console. The opera-tor originally sat between two grain tanks and entered the cab from the rear, next to the motor. Jensen extended the cab 2 ft. forward for a better view of the header, and joined the two grain tanks together to boost capacity from 80 to 120 bu. He cut off the front cab panel, as well as part of the tapered side panels and roof, and installed the Gleaner's floor, welding 2 extra ft. of sheet metal in front of it. He replaced the rear door with sheet metal and built a side
To read the rest of this story, download this issue below or click
here to register with your account number.