You have reached your limit of 3 free stories. A story preview is shown instead.
To view more stories
(If your subscription is current,
click here to Login or Register.)
Grain Wagon Made From Fuel Tanks
"It's a big time saver," says Paul Davidson, Moose Lake, Minn., about the home-made dumping grain wagon he made by fusing together two 265 gal. fuel oil tanks and two 1962 Chevrolet car frames.
Four -wheel, independent suspension allows Davidson to pull the 6 by 6 by 10 ft. rig, fully loaded with 160 bu. of grai
..........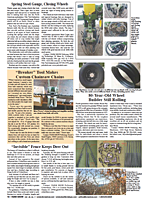
You must sign in, subscribe or renew to see the page.
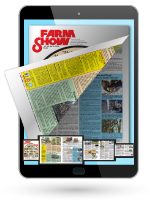
You must sign in, subscribe or renew to see the flip-book
Grain wagon made from fuel tanks WAGONS/TRAILERS Miscellaneous 11-6-11 "It's a big time saver," says Paul Davidson, Moose Lake, Minn., about the home-made dumping grain wagon he made by fusing together two 265 gal. fuel oil tanks and two 1962 Chevrolet car frames.
Four -wheel, independent suspension allows Davidson to pull the 6 by 6 by 10 ft. rig, fully loaded with 160 bu. of grain, be-hind his pickup at road speed.
"A grain truck is too expensive to buy, maintain and license for my small farming operation," says Davidson, an electrician and part-time farmer whose only out-of-pocket cost to build the low-cost grain wagon was for welding rods and gas for the cutting torch he used to transform the two standard, oblong-shaped fuel oil tanks into a flared grain wagon that raises for fast, easy unloading.
In cutting the two tanks, Davidson first made sure they were absolutely empty and safe to torch. After cutting them into pieces (see drawing), he used a mechanical "handyman" high-lift jack to flare the sides to a 6 ft. width at the top. He then welded the two tanks together to create one large 160 bu. capacity tank with sloping, flared sides. He welded an angle iron divider (a bed iron used to hold mattresses in place) to connect the middle sides of the wagon. Diagonal iron straps ù also taken from an old bed ù welded in the inside corners further support the tank.
In making the running gear, Davidson salvaged the front halves of two identical 1962 car chassis, then welded them together nose to nose. He trimmed off both frames at a point just below the radiator and further shortened the frame that forms the rear portion of the running gear.
To strengthen the frames and keep them from twisting under load, Davidson welded a piece of channel iron to heavy framework originally located at point below the cars' oil pans. The original steering arms are welded solid to the frame to keep the four, independently suspended wheels permanently aligned in a straight position. "I can pull it down the road fully loaded at 55 miles an hour and it follows along perfectly," says Davidson.
A long-armed, battery-powered winch, which slips into a bracket permanently mounted on the beefed-up bumper of Davidson's pickup, is used to pick up the front oldie wagon and hoist it into the air for dumping. When hooked to his tractor, Davidson uses a home-made 3 pt. hitch boom to raise and lower the wagon.
For dumping, the rear end of the wagon pivots on a hinge Davidson made by cradling a 4 ft. piece of 1-1/4 in. pipe in the "arms" of a similar length piece of 2-1/2 by 2-1/2 in. angle iron.
In the down position, the grain tank rests on two angle-iron "feet" running length-wise, one on each side along the bottom. Davidson first welded L-shaped mounted brackets along the bottom sides, then welded the long angle iron "feet" to the brackets.
To unload grain, Davidson cut out a 6 by 8 in. oblong-shaped hole at the bottom of the rear end. A sliding metal plate inside the tank covers the hole. The plate is attached to a rod sticking out the back side of the wagon. When the rod is pushed forward, the plate slides up. "The further I push the rod for-ward, the bigger the opening becomes and the faster grain runs out," says Davidson.
The dump wagon is equipped with reflectors but no tail lights. However, its sloping sides allow the pickup's tail lights to shine through for rear visibility. "I don't hesitate to take it down main roads at night," says Davidson.
Contact: FARM SHOW Followup, Paul Davidson, 725 Co. Rd. 12, Moose Lake, Minn. 55767 (ph 218 485-4734).
To read the rest of this story, download this issue below or click
here to register with your account number.