You have reached your limit of 3 free stories. A story preview is shown instead.
To view more stories
(If your subscription is current,
click here to Login or Register.)
Deere Planter Fitted With White Air System
Iowa farmer Bill Fluhrer wanted a more accurate way to plant soybeans with his 1978 8-row Deere 7000 Max-Emerge planter but he didn't want to spend the money for a new vacuum planter.
So he removed the seed hoppers and seed pickup units from the planter and replaced them with seed hoppers designed for a White ai
..........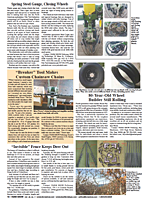
You must sign in, subscribe or renew to see the page.
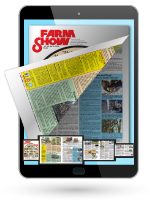
You must sign in, subscribe or renew to see the flip-book
Deere planter fitted with white air system PLANTERS Planters 15-4-21 Iowa farmer Bill Fluhrer wanted a more accurate way to plant soybeans with his 1978 8-row Deere 7000 Max-Emerge planter but he didn't want to spend the money for a new vacuum planter.
So he removed the seed hoppers and seed pickup units from the planter and replaced them with seed hoppers designed for a White air planter along with a White air delivery system including fan, hydraulic motor, tubes, and hoses. He bought the equipment new from a White dealer.
"I like the design of the Deere planter for corn but when I switched to soybeans I'd get uneven seed distribution and population rates. White's air planter is much more accurate in beans. It uses air pressure to hold seed in place against a plate at the bottom of the hopper. There's one plate for corn and another plate for soybeans. A fan driven by a hydraulic motor delivers air through a 4-in. dia. plastic tube that runs the length of the planter, and a flexible rubber hose leads from the tube to each plate. Air holds the seed in place until it reaches the bottom of the plate and drops to the ground. Seed size doesn't matter.
"The planter still uses the base of the Deere row units including openers, seed tube, gauge wheels and packer wheels.
"I increased the size of the planter from 8-row to 12-row by cutting a used Deere 4 row planter in half and adding two row units onto each side of the planter. Both sets of row units are hinged so they can be folded forward for transport. I paid $2,000 for the 4-row planter and spent a total of less than $5,000 to build my air planter. I would have had to pay at least three times as much for a new 12-row Deere vacuum planter."
Fluhrer bolted each White seed hopper to a pair of brackets that he attached to each of the Deere row units. He bolted the fan to a bracket at the center of the planter. The hydraulic motor that drives the fan is operated by the tractor's hydraulic system. The Deere row units were driven from the left side of the planter while the White row units were driven from the right side. To solve the problem Fluhrer moved the drive sprockets over to the opposite side o(each Deere row unit.
"I didn't like the screw-on lids on the White seed hoppers so I tried cutting some of the White and Deere seed hoppers in half, then bolting the top halves of the Deere hoppers to the bottom halves of the White hoppers. However, it didn't work well be-cause I couldn't get the two halves to fit tight so only a few of the hoppers are modified," notes Fluhrer.
Contact: FARM SHOW Followup, Bill Fluhrer, Rt. 1, Charles City, Iowa 50616 (ph 515 228-4662).
To read the rest of this story, download this issue below or click
here to register with your account number.