1988 - Volume #12, Issue #5, Page #27
[ Sample Stories From This Issue | List of All Stories In This Issue | Print this story
| Read this issue]
Farmers 4-WD Tractor Built Piece By Piece
![]() |
Comfort cash crops 600 acres along with his father, Ed, in addition to doing custom work. Since he completed the tractor in 1985, Comfort has averaged 300 hrs. per year on it, pulling a 22-ft. disk and a 5-furrow 18-in. plow. The 10-ft. wide rear-mounted loader bucket is ideal, he says, for mo'ing snow, dirt and manure.
The home-built tractor and cab cost $24,000 to build. It has 15 forward and 3 reverse speeds and an air-operated clutch. The seat and steering wheel console revolve 180? for operation in forward or reverse. Two 50-gal. fuel tanks provide enough diesel fuel for 2 1/2 full days of work. The tractor, which Comfort built during his spare time, is 23 ft. long. The cab is equipped with a heater and air pressurizer. The roof is 11 ft., 11 in. from the ground. According to Comfort, the tractor is relatively light for its size at about 8 tons. As yet, it's never been stuck.
"Everything was done piece by piece, with no plans on paper. I used trial and error, but for the most part there weren't many errors. Most of it went together well. The tractor is a combination of a John Deere industrial loader and an International 2 plus 2 tractor because those are two machines I patterned it after," says Comfort, noting that one big change he made after the tractor was first built was to replace the original 140-hp 471 Detroit diesel engine with a 220 hp Cummins 6-cyl. engine. "I needed more power on hills and for tough ground conditions."
Comfort built the tractor with the two drive axles and transfer case from a 1950 Trojan industrial front-end loader. He mounted the axles, transfer case, and the 15-speed transmission (salvaged from a semi truck) on a frame which he built out of 9 by 2-in. solid steel bars. He says one of the toughest decisions he had to make while building the tractor was deciding where to put the pivot point. He ended up putting it about 1 ft. closer to the rear of the tractor than the front so it would be easier to operate the rear-mounted loader bucket.
The articulated steering joint was built with new parts designed for an International 2 plus 2 tractor. He built the cab from scratch, including controls and steering components, and made the tilt-up engine hood from 10 gal. steel and 1-in. sq. tubing. The tractor's hydraulics come from the industrial loader that supplied the drive axles and transfer case. The loader's front-end loader arms were used to fashion 3-pt. arms at the rear of the tractor and the original loader components are used to raise and lower the 3-pt. The 10-ft. bucket attaches directly to these 3-pt. arms. Comfort had to install new hubs in the tractor wheels in order to fit the drive axles.
Tie rods were installed from the articu¡lated steering joint to the front "steering axle" so the 23-ft. long tractor has a tight, 12-ft. turning radius. "I wanted a tractor that I could use at any time for any job around the farm. This tractor is extremely versatile and handles like a 60 hp. tractor," says Comfort, noting that if were starting out again he would probably use more new parts to reduce maintenance over the life of the tractor. He says he could have used a higher percentage of new parts and still saved money building his own 4-WD. "A new tractor comparable to this one would cost $100,000 or more," he notes.
Contact FARM SHOW Followup, Bob Comfort, Rt. 4, Fenwick, Ontario LOS 1CO Canada (ph 416 386-6151).
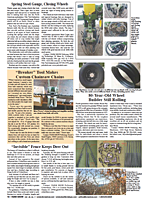
Click here to download page story appeared in.
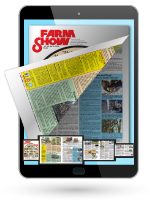
Click here to read entire issue
To read the rest of this story, download this issue below or click here to register with your account number.